Automobile : un traitement de surface ciblé a des avantages mesurables
Entretien
On peut lire actuellement dans la presse que l’UE envisage des pénalités pour l’industrie automobile à partir de 2020. Pour tout véhicule à moteur à combustion nouvellement immatriculé, le constructeur devra verser 95 euros à Bruxelles pour chaque gramme de CO2 dépassant le seuil de 95 g/km. Or, selon le Council on Clean Transportation, les émissions s’élevaient en moyenne à 121 g/km en 2018. Florian Reinle, ingénieur au département Recherche & Développement chez OTEC Präzisionsfinish, nous explique comment les constructeurs automobiles peuvent optimiser davantage encore leurs process de fabrication, tout en réduisant les frottements.
Monsieur Reinle, vous êtes chargé de la question des frottements chez OTEC et vous connaissez parfaitement les problèmes de l’industrie automobile. Y a-t-il des conseils que vous pourriez donner ?
« De par notre expérience et les discussions que nous avons avec les clients, nous savons qu’il y a un levier d’efficacité important à exploiter du côté du lissage ciblé et optimisé des surfaces en friction. Les composants exposés aux frictions de glissement, comme les cames, les segments de piston, les vilebrequins ou les pignons, peuvent être lissés avec précision dans le cadre d’un traitement machine. Dans la mesure où nous apportons une valeur ajoutée supplémentaire avec d’autres traitements avantageux comme l’ébavurage, nous pouvons parler d’une amélioration globale des composants traités ».
Cela semble ambitieux. Pourriez-vous commencer par nous expliquer ce que vous entendez par le lissage ciblé de la surface ?
« Bien sûr ! Nous entendons par là le nivellement de la surface ainsi que la suppression des pics de rugosité et des rainures de traitement. On obtient ainsi une surface isotrope et une rugosité ciblée, décidée d’un commun accord avec le client. Grâce à notre procédé, nous préparons les composants à leur utilisation ultérieure sur le terrain grâce à un apport élevé d’énergie de friction. Nous assurons ainsi une réduction des frottements et de l’usure. La surface présente une couche de cisaillement dans laquelle nous générons des modifications de structure et des tensions propres qui ont pour effet de préconditionner la pièce pour son usage futur. D’un point de vue global, ce traitement final de haute précision réduit les frottements sur la chaîne cinématique : la consommation de carburant s’en trouve diminuée, autrement dit l’énergie motrice mise à disposition est utilisée plus efficacement – avec, à la clé, une diminution des émissions de CO2. »
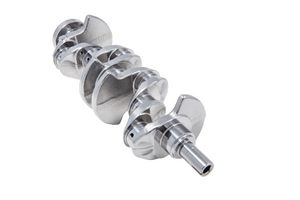
Cela semble très prometteur – pouvez-vous nous dire concrètement quels sont les autres avantages et nous expliquer en quoi les composants bénéficient d’une amélioration globale ?
« Au niveau du traitement lui-même, nous pouvons, grâce aux procédés automatisés, souscrire aux impératifs de fiabilité et de reproductibilité en un temps record, ce qui se traduit par une meilleure maîtrise des coûts. En parallèle, la qualité du produit est améliorée, cela se voit immédiatement sur les pièces. Si vous considérez l’ébavurage ou le rayonnage ciblé, nos solutions présentent des avantages supplémentaires très concrets. Il est évident que le maniement est amélioré et que le montage est facilité lors de l’emmanchement ou de l’introduction de pièces sensibles comme les joints. Il est fréquent que les pièces particulièrement exposées aux frottements et à l’usure reçoivent plusieurs couches de protection. Or, ces couches auront une adhérence beaucoup plus stable et renforcée si la surface a été optimisée auparavant. Il est également possible de procéder à un traitement de lissage après l’enduction.
Autre effet intéressant : la diminution des bruits et des vibrations à bord du véhicule. Il s’agit de toutes les oscillations audibles et perceptibles par les occupants. De la même façon que l’effet induit par la réduction des vibrations et du bruit à bord va bien au-delà des seuls composants, nous pouvons obtenir des effets de synergie importants en procédant au lissage de la surface. Nous en avons un exemple avec l’utilisation de lubrifiants à basse viscosité pour une meilleure efficacité du système tout entier. »
On lit dans la presse que la mobilité électrique serait la solution à adopter par les constructeurs automobiles pour éviter ou limiter les pénalités.
« Oui, le contexte politique général encourage l’arrivée des voitures électriques sur le marché. Toutes les catégories de véhicules ne sont pas concernées de la même façon. Mais les reportages font la plupart du temps référence au fait que l’on fabrique davantage de voitures électriques.
Seulement, construire des véhicules électriques ne suffit pas – encore faut-il qu’ils soient achetés. Et c’est là que la concurrence et les consommateurs entrent en jeu. Quand un automobiliste envisage l’achat d’une voiture électrique, le rapport bénéfices/coût joue un rôle important. À commencer par l’autonomie, le coût à l’achat et les frais d’exploitation. »
La réduction des frictions, mais aussi des bruits et des vibrations joue-t-elle également un rôle pour la mobilité électrique ?
« Le traitement de surface des composants de transmission présente là encore des avantages extrêmement intéressants pour l’automobiliste. Comme pour le moteur à combustion, le fait d’optimiser la surface des composants est un facteur d’amélioration de l’efficacité et des caractéristiques globales des composants. À cela s'ajoute le fait que ce procédé, en soi déjà économique, peut être concentré sur un nombre réduit de composants responsables des pertes par frottement. Résultat : l’automobiliste est gagnant puisqu’il pourra rouler aussi longtemps avec une batterie plus petite (et donc moins chère) ou alors rouler plus longtemps avec une batterie de même puissance. Par ailleurs, les émissions sonores restent un sujet important pour les voitures électriques, puisque les occupants perçoivent désormais certains bruits qui, jusqu’à présent, étaient couverts par le moteur à combustion. »
Pourquoi les constructeurs automobiles devraient-ils envisager l’utilisation de la technologie OTEC ? Quel avantage auraient-ils à le faire ?
« Les clients du secteur automobile qui travaillent déjà avec OTEC Präzisionsfinish en production se félicitent bien sûr des avantages mentionnés plus haut concernant les pièces, mais aussi des avantages liés au process. En effet, le procédé de polissage à flux continu développé par OTEC fonctionne sans acide : un avantage pour la santé et l’environnement. Comparé aux autres procédés de finition, il a comme autre avantage d’être plus économique. Et avec des temps de traitement de 90 secondes en moyenne, il est le procédé de tribofinition le plus rapide sur le marché.
Pour parvenir à ce résultat et faire la différence par rapport aux autres techniques, il utilise des forces de traitement élevées et l’énergie de frottement importante dans la machine. Le polissage à flux continu consiste à fixer les pièces dans un support avant de les plonger dans une cuve en rotation remplie d’abrasifs ou d’agents de polissage. Le mouvement de travail à proprement parler est assuré à la fois par le flux d’abrasifs ou d’agents de polissage et par la pièce elle-même en rotation. Cette technologie permet d’obtenir un enlèvement de matière plus ciblé et plus rapide qu’avec n’importe quelle autre machine de tribofinition. La SF a été spécialement conçue en pensant aux applications pour lesquelles il n’existait pas de procédés satisfaisants. La reproductibilité et le temps de traitement sont des facteurs déterminants et font partie des exigences formulées par l’industrie automobile.
Grâce aux forces de traitement importantes à l’œuvre dans nos solutions, nous sommes en mesure de traiter les géométries fines de manière efficace, avec des abrasifs et des agents de polissage appropriés. Il est même possible d’intégrer nos solutions à une ligne de production grâce au chargement automatique et à la simplicité d’adaptation aux cadences. »
Merci beaucoup, Monsieur Reinle !
Elle tourne comme une horloge : automatisation de la série SF avec le système de chargement robotisé (RLS)
Lorsqu’il s’agit de traiter de grandes quantités de pièces, la rapidité de chargement et de préparation devient un facteur d’efficacité essentiel. Pour y parvenir, le chargement est automatisé à l’aide de robots (SF RLS, voir illustration à gauche). Les machines de la Série SF Automation peuvent être commandées avec ou sans technologie PULSFINISH et conviennent notamment pour les lignes de production cadencées. En fonction des besoins, les machines peuvent au choix être préparées pour le chargement automatique ou être équipées du chargement automatique intégré. Le caractère modulaire de la machine facilite l’adaptation aux cadences. La SF Automation peut ainsi être intégrée sans problème à une ligne de production.
Traitement gratuit des échantillons
Mettez-nous à l’épreuve et envoyez-nous vos échantillons : dans notre Centre de finition interne, nous procéderons pour vous à une analyse gratuite pour définir le processus à mettre en œuvre. Pour en savoir plus : Traitement des échantillons dans le Centre de finition interne >>