The GYSIN AG
The success story between OTEC and GYSIN AG.
GYSIN AG, based in Itingen, Switzerland, has stood for Swiss precision and reliability for over 70 years. The company specializes in the tailor-made manufacture of gears and gearboxes and supplies demanding industries such as the automotive, aerospace and medical technology sectors. From planetary and worm gears to customer-specific solutions, GYSIN AG offers high-quality products - based on state-of-the-art technology and a dedicated team of experts who meet individual customer requirements. However, ensuring the highest surface quality in gear production presented the company with challenges.
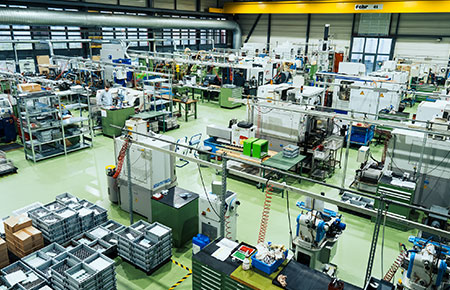
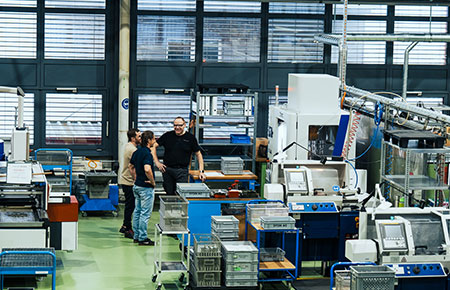
THE CHALLENGE
Before working with OTEC, GYSIN AG relied on time-consuming processes for the surface treatment of gears, such as manual polishing of worm gears. Although these processes worked, they were far from an optimal solution and slowed down production. Manual polishing brought further problems: uneven results in hard-to-reach areas such as small recesses and a high labor input. In addition, the use of water and abrasives during processing led to rust formation - with negative effects on efficiency, product quality and the environment. Increasing production costs and quality requirements made a more efficient and sustainable solution necessary.
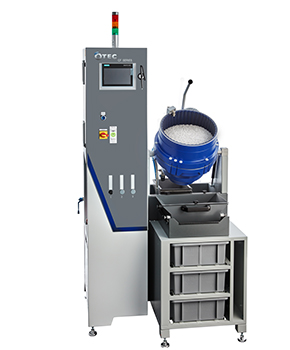
THE TURNAROUND THANKS TO OTEC TECHNOLOGY
To overcome these challenges, GYSIN AG turned to OTEC Präzisionsfinish GmbH, a leading provider of innovative surface finishing. With its extensive expertise and versatile machine portfolio, OTEC integrated two machines for processing bulk goods and a further system for high-gloss polishing in the piece goods sector into GYSIN's production process:
- CF-18 oil
- CF-50 oil
- DF-3 HD dry
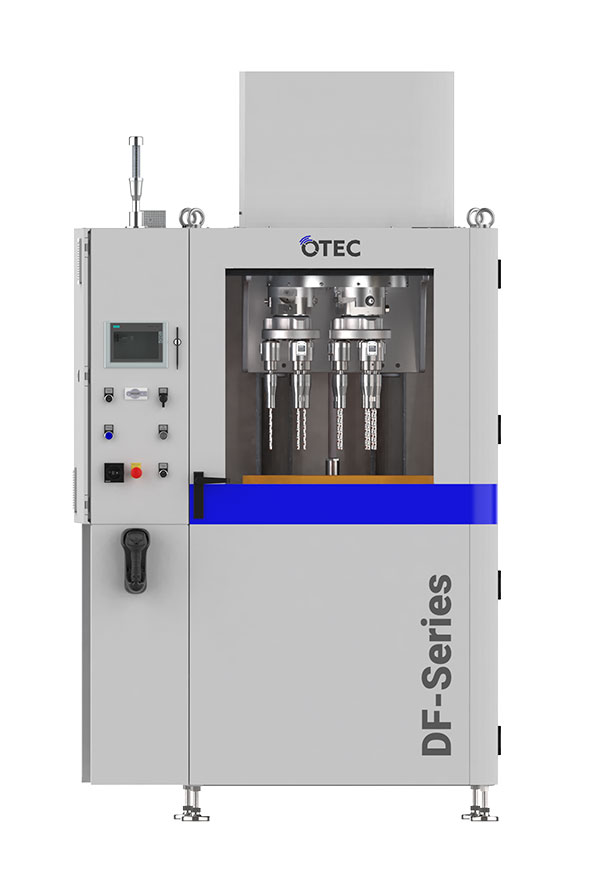
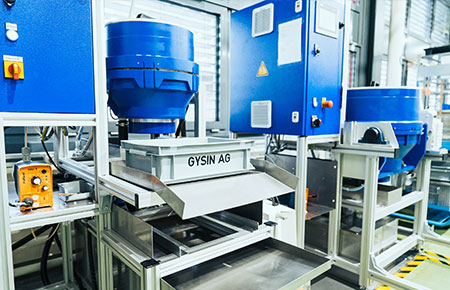
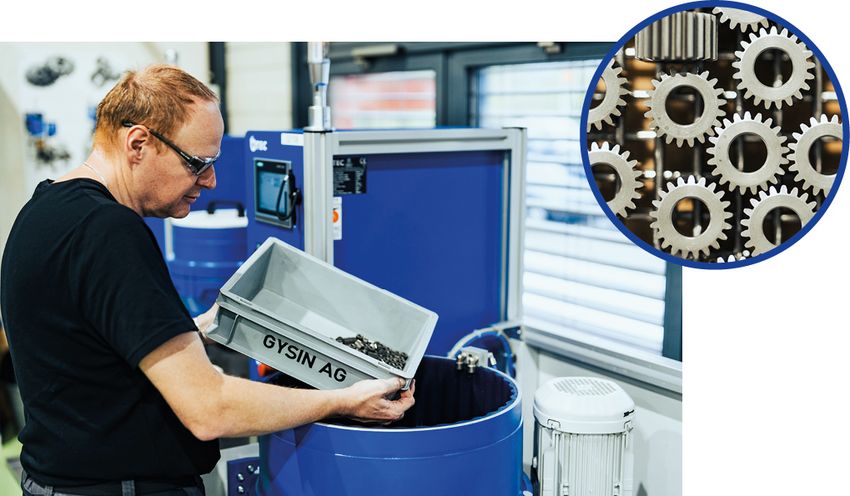
These machines brought about a real transformation: they enabled GYSIN AG to automate and optimize machining processes while reducing the environmental impact.
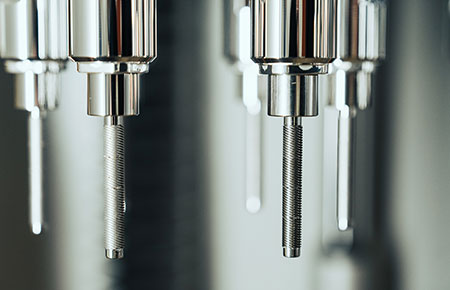
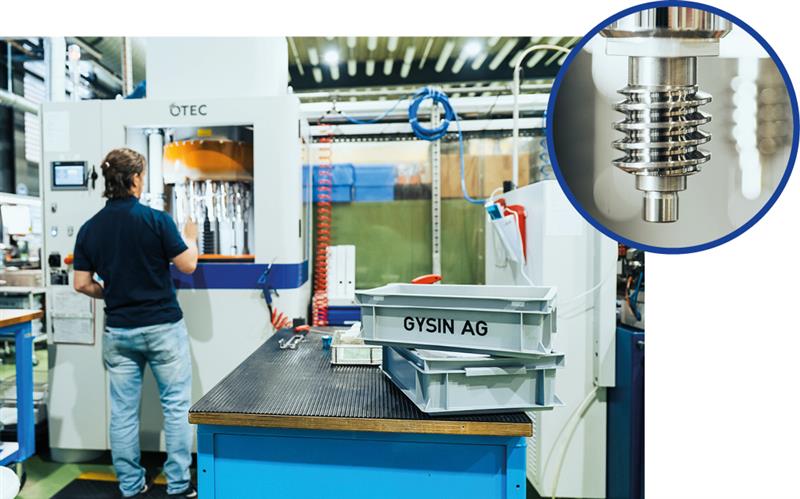
MEASURABLE RESULTS AND BREAKTHROUGH BENEFITS
The implementation of the OTEC machines immediately brought noticeable improvements to the company's production process:
- Significant time savings
The processing time for gears fell from the previous 8-9 hours to just 30-50 minutes. This increase in efficiency accelerated production and created capacity for other important tasks. - Uniform, flawless polishing
Worm wheels were polished with the utmost precision down to the smallest indentations - a quality that could not be achieved using manual methods. - More sustainability
The use of OTEC's CF-Technology eliminated the need for water, abrasives and abrasive sludge - reducing waste, simplifying disposal and protecting the environment. - Easy handling and cleanliness
The user-friendly operation of the OTEC machines not only improved the working experience, but also ensured significantly more cleanliness in the workplace.
CUSTOMER SATISFACTION AND LONG-TERM PARTNERSHIP
The positive results were convincing across the board. Managing Director Renè Hãnni emphasizes:
„OTEC's support and advice during and after the project were excellent. The quality of the solution completely convinced us."
The collaboration between OTEC and GYSIN AG impressively demonstrates how innovative technologies can redefine manufacturing processes. With OTEC's solutions, GYSIN not only increased efficiency, but also underlined its own commitment to the highest product Quality and sustainability.
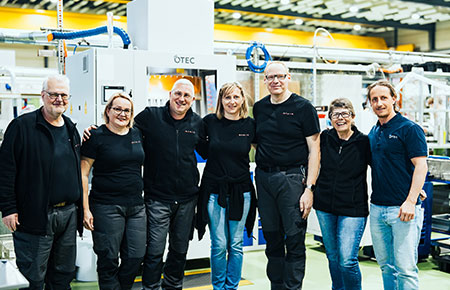
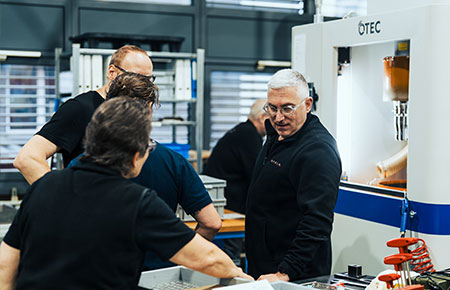
STANDARD FOR THE INDUSTRY
Thanks to its partnership with OTEC, GYSIN AG is setting new standards in the world of mass parts processing. This success story impressively demonstrates the potential offered by modern surface technologies - for greater efficiency, lower environmental impact and uncompromising quality.
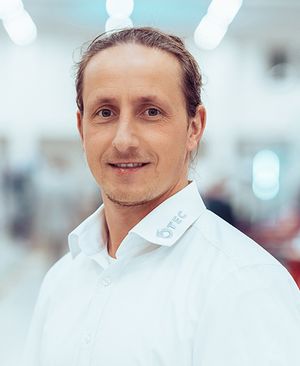