Aerospace
As tough as it gets for Surface requirements
The aerospace industry faces demanding challenges, as highly efficient and extremely reliable technology is essential. At the same time, the path to a more sustainable future requires significant changes. The European alliance ACARE has set ambitious goals, including:
- a 75% reduction in carbon dioxide emissions by 2050,
- a 90% reduction in nitrogen oxides,
- and a 65% reduction in noise.
Download
Reducing friction in engines plays a central role in achieving these goals, with the smoothing of functional surfaces being crucial.
Unmatched Precision with OTEC Mass Finishing Machines
Efficient design in aerospace requires tight tolerances and minimal process deviations. Our innovative Mass Finishing Machines provide the ideal solution, offering stability, repeatability, and fully automated processes that meet the demands of leading OEM, Tier 1, and Tier 2 manufacturers. Our systems not only enhance process quality but also deliver significant advantages over conventional methods, actively contributing to the achievement of ACARE goals.
Our Core Competencies
- Super Finishing and Ultra Polishing: Homogeneous smoothing to achieve minimal surface roughness.
- Rounding and Deburring: Consistent and repeatable edge rounding for optimal functionality.
- Custom Solutions: Development of tailored processes for individual requirements.
- Safe Technology: No use of hazardous chemicals.
- High-Precision Surface Processing: Microscopic lubrication pockets minimize the risk of lubricant film breakdown.
- Improved Quality: Significantly better surface isotropy with reduced roughness peaks.
- Durability through OTEC Processing: Reduced wear, no break-in phase required, longer oil service life.
- Reliability: Lower risk of micropitting.
OTEC processes ensure the highest precision and repeatability for large and heavy parts. They offer an economical, stable, and sustainable alternative to traditional post-processing methods, setting new standards in quality and efficiency.
Smoothing | Polishing
Blades, guide vanes, blisks, impellers, gears, valve parts, nozzles
Using Stream Finishing and Disc Finishing Processes, surfaces of compressor blades, guide vanes, blisks, and gears are smoothed to Ra 0.01, enhancing aerodynamics and performance. For gear components, smoothing tooth flanks and rounding edges reduce friction and wear, while specially created lubrication pockets ("lubrication valleys") ensure higher efficiency and safe operation. With OTEC processes, highly hardened gears achieve roughness values as low as Ra 0.07.
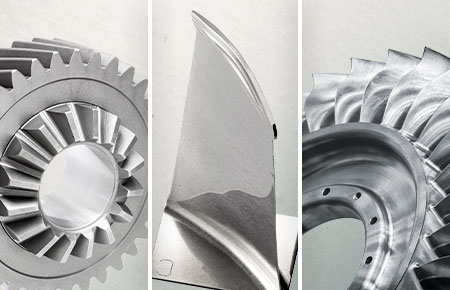
Deburring | Rounding
Turbine blade roots, compressor and turbine discs, gears, nozzles, impellers, fittings, hydraulic and fly-by-wire components
OTEC machines from the SF and CF-Series offer precise edge rounding and deburring, ideal for single parts and bulk processes. With repeatable stability and cost efficiency, they handle tight tolerances and challenges like sharp edges and burrs. Stream Finishing Processes, certified by several OEMs such as GE Aerospace (P11TF15 Edge Treatment Process Control, …), guarantee the highest quality for demanding components.
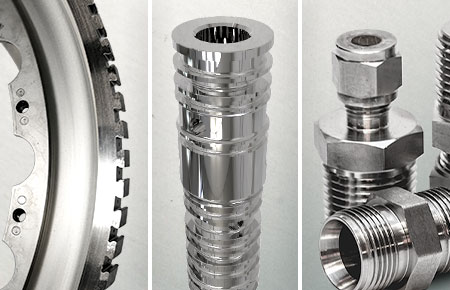
Additional Applications
Coated parts, additively manufactured parts, landing gear components
Very large or newly manufactured components, which were often manually processed or finished using outdated methods like trough vibration and chemically accelerated mass finishing, benefit from OTEC’s innovative processes. Parts up to 900 mm in diameter, 650 mm in length, and weighing 200 kg can be processed with precision and the usual OTEC quality.
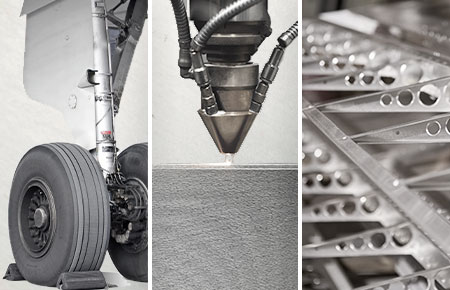
Efficiency and Sustainability
OTEC machines offer process times up to 40 times faster than chemically accelerated processes. They operate cost-effectively, stably, and without the need for expensive and environmentally harmful acids or hazardous chemicals. This makes the processes not only more efficient but also more environmentally friendly.
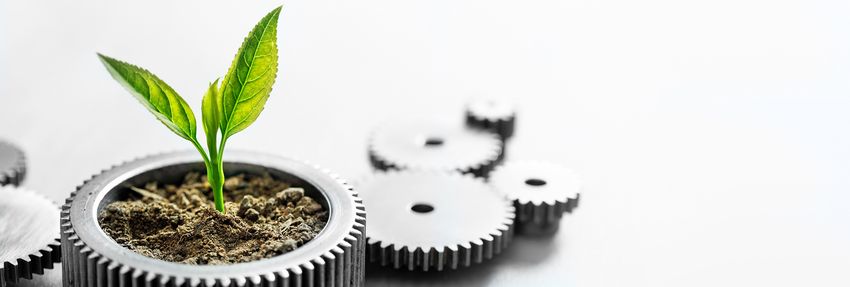
Overview of OTEC Machines
For Individual Parts
SF-HP-Series
The SF-HP is designed for surface processing of large and heavy workpieces up to 200 kg. more
SF-Series automation
Suitable for automatic workpiece loading, ideal for cycle-bound line production. more
SF-Series Manual
Suitable for manual workpiece loading, ideal for small series or lines without cycle time requirements.more
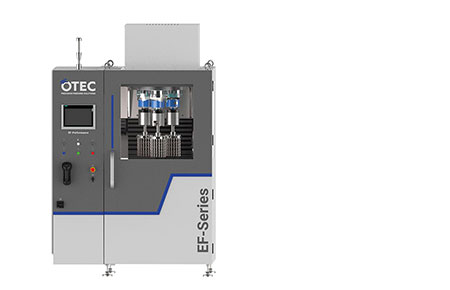
EF-Performance
High-quality polishing and smoothing for complex geometries.more
For Bulk Material
![[Translate to Russian:] [Translate to English:] CFT, CFCA, CF](/fileadmin/uploads/Produkte/Gleitschleifen/Tellerfliehkraftanlagen/3_Serie-CF-Standard-Behaelter-gekippt.jpg)
CF-Series
Perfect for fast and flawless surface processing of bulk parts.
more