COMPONENTI PER OCCHIALI
Esclusivo sistema di intercapedine a scorrimento per una lavorazione senza danni
Gli occhiali vengono indossati principalmente come ausilio ottico per correggere difetti della vista ed errori di posizione dell'occhio. In questo caso, si parla di occhiali “correttivi”. Inoltre gli occhiali pos-sono essere utilizzati per proteggere gli occhi da agenti esterni, lesioni o sollecitazioni. Ma l'occhiale è usato anche come accessorio di moda.
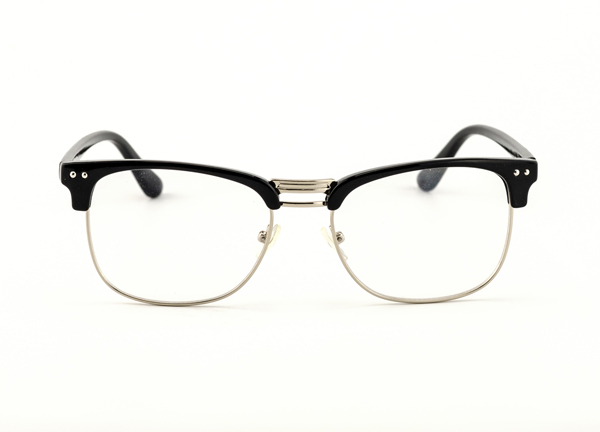
I due elementi principali di un paio di occhiali sono le lenti e la montatura. La montatura, a sua volta, è formata da diversi componenti più piccoli, come le aste, i terminali, le cerniere, i cerchi, il nasello e il ponte nasale. Il ponte nasale è un componente fondamentale, in quanto collega la montatura tra le lenti e garanti-sce una distribuzione uniforme del peso. Naturalmente nella produzione degli occhiali vengono impiegati materiali di alta qualità. Le montature in metallo sono infrangibili, resistenti ai graffi e mettono in risalto il design dell'occhiale. Tuttavia, per garantire il massimo comfort, durante la produzione il ponte nasale deve essere sottoposto a una sbavatura e un arrotondamento completi.
I piccoli componenti per occhiali, come le cerniere, i ponti nasali e i giunti possono essere sbavati, levigati e lucidati nelle macchine CF di OTEC grazie a un processo speciale che li prepara anche per le lavorazioni successive. Per rimuovere le bave del processo di produzione dai pezzi, viene utilizzato un materiale in ceramica ad elevata forza abrasiva, seguito da un abrasivo plastico che esegue la le-vigatura finale. Affinché i componenti degli occhiali rimangano puliti durante il processo, viene ag-giunto un composto che risciacqua i residui dell'abrasione e protegge dalla corrosione. Uno speciale granulato in guscio di noci garantisce la successiva lucidatura dei componenti. La lucidatura ad alta brillantezza consente di ottenere una superficie liscia, che rappresenta un criterio importante soprat-tutto nell'ottica.
Le macchine OTEC CF utilizzano la finitura a disco centrifugo, una tecnica di smerigliatura altamente efficace. Qui i pezzi vengono inseriti nel materiale di finitura e mossi mediante un disco rotante che è separato dal contenitore da uno spazio regolabile. In questo modo, il materiale abrasivo raggiunge un flusso toroidale. I componenti degli occhiali vengono lavorati in modo preciso e costante per effetto delle diverse forze centrifughe.
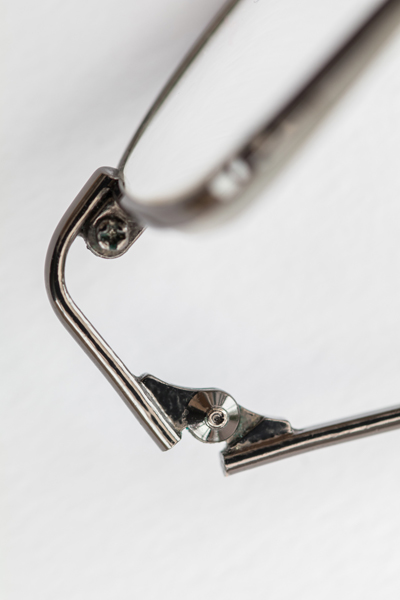
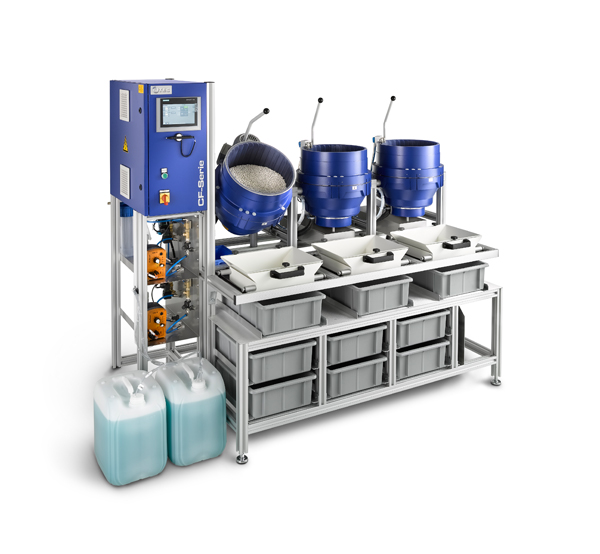
Nelle macchine per finitura a disco centrifugo di OTEC, i componenti degli occhiali possono essere lavorati come materiale sfuso, conseguendo risultati ottimali. Inoltre l'alta velocità di rotazione e l'e-levata velocità relativa riducono i tempi di lavorazione e garantiscono un maggiore rendimento. Gli in-serti rotondi del disco assicurano una lavorazione delicata dei componenti degli occhiali. I compo-nenti piatti e piccoli non aderiscono al bordo del disco durante il processo; in questo modo, è possibi-le ottenere una lavorazione completa.
Diversamente dai processi di lavorazione tradizionali, con le macchine per finitura a disco centrifugo di OTEC è possibile lavorare componenti in metallo anche molto piccoli senza danneggiarli. Grazie all'esclusivo sistema di intercapedine a scorrimento, lo spazio tra il disco rotante e il contenitore fis-so può essere ridotto a zero. Così i pezzi non rimangono incastrati nello spazio, i danni ai componenti degli occhiali si riducono ed è possibile ottenere una superficie liscia e levigata. Il vantaggio offerto dal sistema di intercapedine a scorrimento consiste in una lavorazione senza danni, ideale per i componenti per occhiali di piccole dimensioni, come ponti nasali e cerniere.
Per la lavorazione è altresì possibile utilizzare abrasivi a grana molto fine. L'ingegnosa geometria del contenitore riduce i tempi di lavorazione fino al 30% rispetto alle macchine tradizionali impiegate per le stesse applicazioni. Grazie al processo di lavorazione OTEC, i vostri componenti per occhiali avranno una superficie perfetta ed estremamente lucida.