Optimal tool processing? Stream Finishing (SF) compared with Electro Finishing (EF)
Florian Reinlea, Maximilian Eckla, Luca Wölka, Carlos Barbado Fernándeza, Lukas Göhlera
aOTEC Präzisionsfinish GmbH, Straubenhardt
Abstract
Precise rounding and smoothing of tool cutting edges is crucial for a longer service life and reliable machining processes. This report compares two established post-processing methods for tools: the mechanical Stream Finishing Process and electrochemical Electro Finishing. Stream Finishing allows high, precisely controllable material abrasion through abrasive processing and is particularly suited for larger and mechanically more robust tools. Electro Finishing, on the other hand, uses anodic material removal in an electrolyte in order to smooth delicate and complex-shaped workpieces without mechanical stress. Both methods achieve defined cutting edge rounding, yet they differ in how they work and their results: Stream finishing can produce an adjustable C factor from ~0.5 to ~2.0 and, with suitable parameter settings, can induce significant compressive residual stress and hardening in the edge zone. Electro Finishing, on the other hand, achieves extremely low roughness on workpieces without impurities getting in and without mechanical deformation or shearing of the microsurface. These properties are beneficial particularly for micro-tools and precision tools. This report illustrates the specific strengths of both processes and concludes by showing that a combined use of stream finishing and Electro Finishing can be a very promising approach in practice for getting the best results during tool processing.
Introduction
Cutting edge rounding and homogenisation of cutting edges are key measures for increasing tool life. Both mechanical mass finishing, especially the Stream Finishing Process, and Electro Finishing offer options for targeted edge preparation. While the Stream Finishing Process is suitable for larger tools due to its high material removal rate and flexibility, Electro Finishing shows its strengths with delicate tools that would not withstand mechanical forces. This report describes both processes in detail, compares their advantages and disadvantages, and looks at their areas of application.
1. Mechanical stream finishing: Stream Finishing Process
The Stream Finishing Process is based on a rotating process container filled with abrasive granulate, into which the workpiece is immersed. Setting specific process parameters allows controlled cutting edge rounding with an adjustable C factor of between 0.5 and 2.0. Typically, a C factor greater than 1 is preferred to ensure a longer service life and improved chip formation.
1.1 Process description and technical implementation
Stream Finishing is based on a rotating process container filled generally with abrasive grinding or polishing granulate, into which a workpiece that is secured according to specifications is immersed (Fig. 1).
OTEC Präzisionsfinish GmbH has enhanced this process to achieve its Stream Finishing (SF) Process. The precise rotation of the workpiece holder around its axis allows a wider range of processing options. Many combinations of rotation around the axes are possible. The workpiece holder can also be rotated in a pulsed fashion (i.e. highly dynamic alternating rotation) around the longitudinal axis. The immersion depth and immersion angle, and the resulting wall and floor clearance are key parameters for setting the efficiency of the process. The flow can be adapted very flexibly to the requirements of the specific workpieces using the process parameters. This allows uniform surface processing and targeted edge and cutting edge preparation.
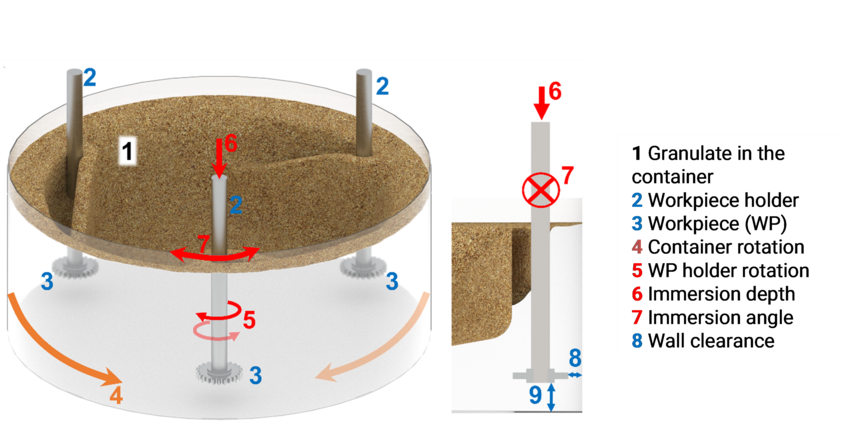
The friction energy results from the pressure and motion of the granulate relative to the workpiece. This introduction of energy during Stream Finishing is beneficial for surface conditioning [1] and allows shear stress-induced microstructural changes, which can also lead to compressive residual stress induction in the case of high-speed steel (HSS). Many years of practical use show that the Stream Finishing Process offers high reproducibility and can be flexibly adapted to different tool geometries. Innovations such as digital modelling using DEM simulation allow further potential for development with regard to these strengths.
1.2 DEM simulation as a virtual model
Mass Finishing Processes such as Stream Finishing can be simulated using the Discrete Element Method (DEM). Unlike conventional FEM or CFD methods, DEM simulates individual, freely moving particles that can interact with each other and with boundary walls [2]. There is no need for a static computational grid, which would have to be continuously adjusted for dynamic movements. In each time step, the interaction of each particle with potential adjacent particles and the walls (e.g. the workpiece surface) is calculated. The selected time step is small enough to ensure that every particle movement is precisely captured. This eliminates the need to deal with convergence problems of an implicit solver – an advantage of explicit simulation methods. The forces between particles and the wall are calculated from relative movement, mass and inertia, and tangential friction forces and adhesion forces are added. In the normal contact model, the force increases as the number of overlapping particles increases; the spring-damper model produces a rebound as soon as the counterforce decreases. Energy absorption based on the coefficient of restitution is also modelled in this step. This simulation method is suitable both for complex particle shapes, near-spherical shapes as well as for idealised spheres. Abstraction as a sphere requires less calculation effort so that millions of particles can be simulated. A rolling resistance model is therefore available for near-spherical shaped particles to enable their efficient and at the same time realistic simulation.
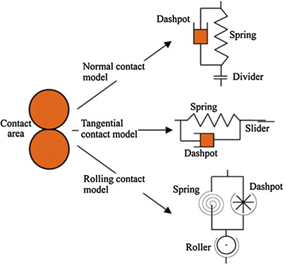
The quantitative and visual evaluation options of a DEM simulation are many and varied. For validation simulations or machine load analyses, resulting forces or bending moments are used. These are calculated based on the total local normal and tangential forces on the workpiece and on the holder. For application-related optimisations, the relative speed of the particles to the workpiece surface is particularly interesting, as well as the product of local pressure and relative speed. Neither sufficient pressure nor high speed alone allows effective processing – only the combination of both variables provides a suitable key performance indicator for the processing effect. This variable is called the P×V value and represents a performance equivalent of the process [4].
2. Electro Finishing: Smoothing by means of anodic material removal
Electro Finishing allows precise surface processing by means of anodic dissolution of the metal in electrolytes [6]. It offers advantages particularly for delicate tools or materials (e.g. hard metal) as it exerts virtually no mechanical stress on the workpiece.
2.1 Process description and technical implementation
Electro Finishing is an electrochemical process for reducing the roughness of metallic surfaces by means of targeted anodic dissolution of the material in an electrolyte. Unlike mechanical polishing, Electro Finishing does not require any abrasives, which change the crystalline micro-structure or could become engrained in the surface. It is therefore possible to smooth delicate and complex-shaped workpieces without impurities getting in and without mechanical deformation. These advantages have led to increasing industrial use in recent years, particularly for medical implants and in dentistry.
Although the principle of smoothing a surface by means of anodic dissolution was already described at the beginning of the 20th century by Beutel [5] and Spitalski [6], most of the Electropolishing solutions that are still used today are based on the studies carried out by Figour [7] and Jacquet [8] in the 1930s. Systematic investigations during the following decades show that Electro Finishing can be attributed to the formation of a diffusion-limited layer, through which micro roughness, in particular, is preferably removed [9 – 19].
To get the best possible smooth and shiny surface, the Electro Polishing process, the electrolyte and the workpiece material must be well matched [18, 19]. There are numerous electrolyte systems – ranging from mixtures of strong acids, neutral and alkaline solutions to non-aqueous solutions [20]. These are generally characterised by the fact that the liquid electrolyte solution dissolves the workpiece by applying anodic potential, thereby removing material and smoothing the surface. This is why these are referred to as polishing baths. The disadvantages of these baths, however, are that they are often highly corrosive, contain harmful substances, and produce a lot of gas at the electrodes. In addition, shielding of the electric field means that inner areas of complex-shaped components are processed less effectively or are not processed at all.
Mixtures containing solid particles and liquid electrolyte, which allow much better and more homogeneous processing of the surface, are an alternative approach to this [21, 22]. This means that more environmentally friendly and less corrosive chemicals can be used than with conventional processes in polishing baths, for example.
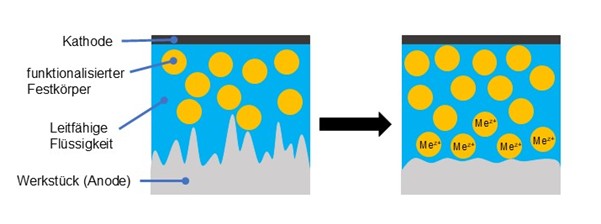
2.2 Advantages and limitations
An important material-specific aspect during Electro Finishing of hard metal tools is cobalt leaching – the selective dissolution of the cobalt binder phase. While some experts consider this a disadvantage, others see it as improving adhesion for subsequent PVD coatings. Reducing cobalt leaching to a minimum is currently being examined.
Another advantage of Electro Finishing is the possibility of smoothing existing PVD coatings and thus achieving a better final surface. This is done by dissolving the metal atoms, whereby the covalent partner in the compound oxygen or nitrogen is gassed out. Since these coatings are often very resistant to mechanical abrasion, this electrochemical material removal method is particularly beneficial here. Mechanical abrasion can cause so-called droplets (melt spatter) of the coating to break off. This does not happen during plateau-like material removal by means of Electro Finishing.
Stream finishing with targeted process control allows gentle removal or smoothing of droplets. Where droplet breakage is acceptable, this can be used specifically to reduce surface roughness peaks particularly efficiently.
The low micro roughness that can be achieved using Electro Finishing means that the adhesion of the cutting contact partners is reduced, allowing optimal transmission of force. Compared with Stream Finishing, Electro Finishing typically achieves C factors of between 0.7 and 0.9, making it ideal for applications requiring a symmetric edge radius or waterfall-effect rounding.
Micro-tools, tools with sharp blades (danger of chipping), tools with a specific mechanical flow shadow, HSS taps, and PVD-coated tools are particularly suitable components.
3. Comparison of the processes
3.1. Technical comparison
Feature | Stream Finishing (mechanical) | Electro Finishing (electrochemical) |
Material abrasion | High, targeted control | Low, precise control |
C factor | 0,5 - 2,0 | 0,7 - 0,9 |
Used on | Large tools | Small, delicate tools |
Homogenisation | Very good | Excellent |
Micro roughness | Significantly reduced | Minimal |
Smoothing of PVD coating | Good | Very good |
Table 1 Comparison of the technical possibilities based on expert knowledge within OTEC Präzisionsfinish GmbH |
3.2 Areas of application
- Stream Finishing is ideal for applications requiring high material abrasion and for larger tools that require precise processing.
- Electro Finishing is ideal for delicate tools or for tools that are already coated as it allows excellent smoothing with minimal material removal.
4. Practical examples and case studies
4.1 Use in the tool industry
In industrial use, the Stream Finishing Process is often used for milling tools, drill bits, taps, and much more, particularly to extend their service life. Electro Finishing, on the other hand, is increasingly used on micro-tools in the medical devices industry and in the watchmaking industry. Fig. 4 shows an electropolished tool surface as an example. You can see signs of cobalt leaching and there is more abrasion in the cobalt binder phase in the hard metal than in the tungsten carbide phase. You can also see the extremely low micro roughness as well as the tribologically good plateau-like surface. This underlines the added value of post-processing even for precision tools that are already coated.
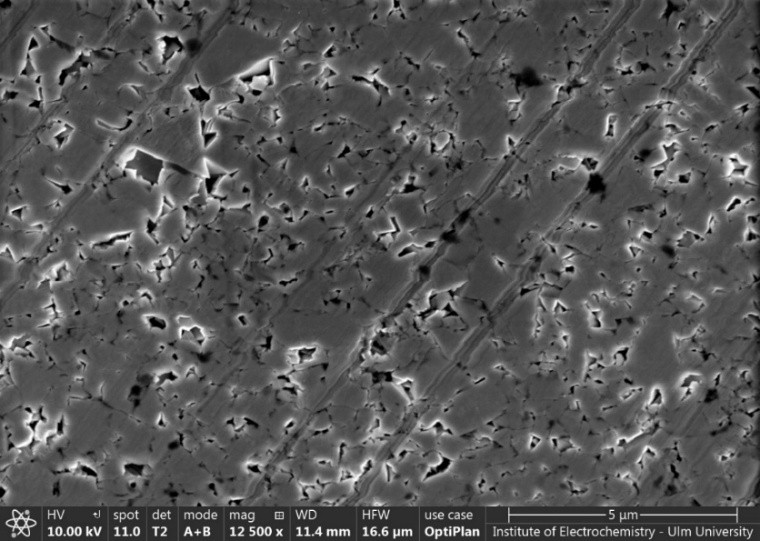
With regard to Stream Finishing, as documented in extensive testing with solid carbide milling tools carried out by Zeilmann et al. (2024), a significant improvement in tool life can be expected with tools prepared using stream finishing [23].
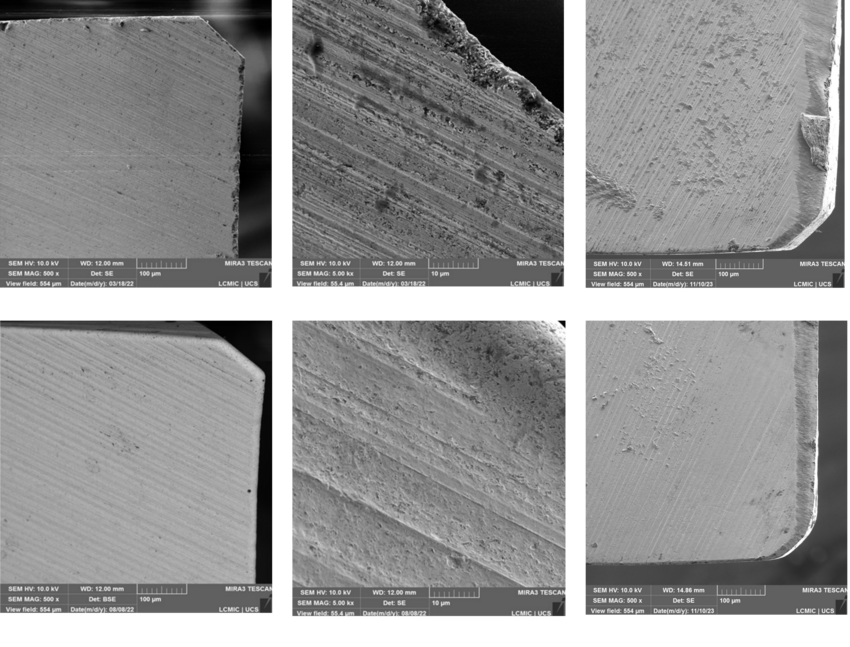
The observed increases in tool life show an expected dependency on the material being machined, but vary significantly: While an increase of around 30 % was achieved with tempered tool steel, the increase for aluminium was up to 400 %. It is important to bear in mind here that the cutting edge rounding of around 20 µm used here was not ideal for processing steel – it tended to be too high for this. Higher rounding values increase plastic material displacement and the cutting forces, which has less of a negative effect on less tough materials like aluminium [24, 25]. A reduced adhesion tendency (see Fig. 6) and better heat dissipation were also observed during testing.
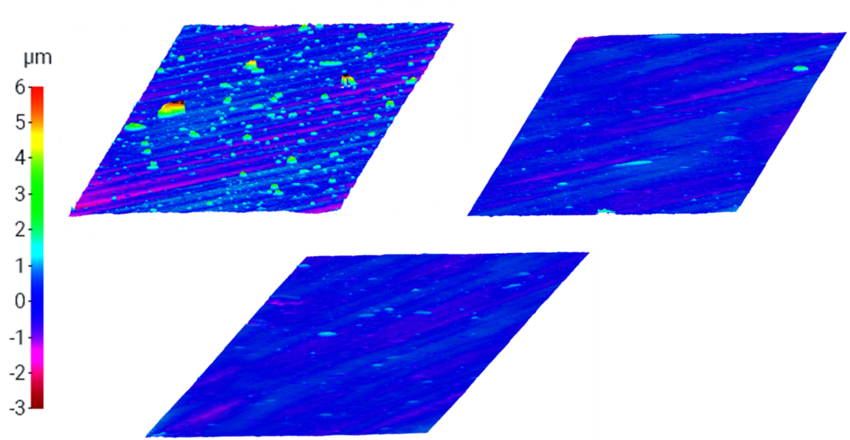
With regard to Electro Finishing, an application example using a tap shows that the roughness (surface parameter Sp) of TiN-coated tools can be reduced by up to 80 %, significantly improving tool performance. A comparison of the processed surface compared to the initial state shows significant smoothing of the droplets, which were almost completely removed after only 2 minutes. The roughness was reduced by almost 70 % while it took another 60 seconds to reliably remove all the droplets, which meant an 80 % reduction in the surface peak parameter Sp in just 3 minutes. The plateau-like material removal can also be seen (Fig. 6, centre).
In summary, these examples show in particular how Stream Finishing is suitable for improving geometry before applying the coating and how post-processing is suitable for achieving the ideal application surface after coating using Electro Finishing. This means that potential disadvantages of the new Electro Finishing technology for tools can be avoided while still benefiting from the advantages.
4.2 Economic considerations
Another relevant aspect is the cost-effectiveness of the processes. While Stream Finishing Units require higher initial investment, the unit costs per processed component are comparatively low due to short cycle times. Electro Finishing, on the other hand, requires special electrolyte solutions and more time for comparable material removal, resulting in higher variable process costs per workpiece. In applications with a high throughput and mechanically robust workpieces as well as in fully automated applications, SF is therefore often more cost-effective, while Electro Finishing Units currently have distinct advantages for small series, intricate parts or particularly for finishing after coating.
5. Conclusion and outlook
Both processes – Stream Finishing and Electro Finishing – each have specific advantages. Stream Finishing is ideal for applications in which high material removal and significant edge rounding are required, or where larger tools have to be processed efficiently. Wherever it is already established, SF is still an excellent choice for tool and edge preparation and for targeted C factor modification.
Electro Finishing, on the other hand, is ideal for delicate or complex-shaped tools and for tools that are already coated as it allows excellent smoothing with minimal material removal. In many cases, a hybrid approach to using both processes – Stream Finishing first, then Electro Finishing – is the best solution for achieving both macroscopic forming and microscopic smoothing. In the future, new developments in the electrolyte formulation of Electro Finishing could help to further minimise cobalt leaching. Likewise, new process strategies and parameter optimisations could adapt the Stream Finishing Process to specific requirements in a more targeted way (e.g. adapted edge profile for different materials). The combination of digital simulation and experimental optimisation will continue to play a key role in the development of advanced tool processing. Ultimately, this comparison shows that neither the mechanical nor the electrochemical process alone is universally superior – it comes down to the right selection and combination for the task in question in order to achieve the best tool performance. Comprehensive expertise both in mechanical and electrochemical finishing increases the likelihood of working out the best combination of processes for each specific application.
References
[1] A. Kacaras, J. Gibmeier, F. Zanger, V. Schulze, Influence of rotational speed on surface states after stream finishing, 4th CIRP Conference on Surface Integrity, 2018
[2] Cundall, P.A., A computer model for simulating progressive, large-scale movements in blocky rock systems. 1971
[3] Zhao T., Coupled DEM-CFD Analyses of Landslide-Induced Debris Flows. 2017
[4] F. Zanger, A. Kacaras, P. Neuenfeldt, V. Schulze, Optimization of the stream finishing process for mechanical surface treatment by numerical and experimental process analysis, CIRP Annals, 2019
[5] E. Beutel in Veröffentlichungen der Chem. Tech. Abteilung des Kais. Königlichen Lehrmittelbüros, Wien, 1907.
[6] Spitalsky, Deutsches Patent Nr. 225.873, 1910.
[7] H. Figour, P. A. Jacquet, Französisches Patent Nr. 707526, 1930.
[8] P. A. Jacquet, Nature 1935, 135, 1076.
[9] J. Edwards, J. Electrochem. Soc. 1953, 100, 189C.
[10] W. C. Elmore, J. Appl. Phys. 1939, 10, 724.
[11] C. L. Faust, J. Electrochem. Soc. 1949, 95, 62C‐72C.
[12] D. R. Gabe, Metallography 1972, 5, 415.
[13] K. B. Hensel, Met. Finish. 2002, 100, 425.
[14] P. A. Jacquet, Metall. Rev. 1956, 1, 157.
[15] C. Wagner, J. Electrochem. Soc. 1954, 101, 225.
[16] J. Toušek, Corros. Sci. 1975, 15, 113.
[17] D. Landolt, Electrochim. Acta 1987, 32, 1.
[18] G. Yang, B. Wang, K. Tawfiq, H. Wei, S. Zhou, G. Chen, Surf. Eng. 2017, 33, 149.
[19] W. Han, F. Fang, Int. J. Mach. Tools Manuf. 2019, 139, 1-23.
[20] M. Buhlert, Electrofinish - elektrolytisches Glänzen, Glätten und Entgraten von Edelstahl, Stahl, Messing, Kupfer, Aluminium und Titan, 2. Aufl., Leuze Verlag, 2017.
[21] N.K. Krioni, A.D. Mingazhev, V.A. Gafarova, J. Phys.: Conf. Ser. 2021, 1891, 012028.
[22] Verdooren, A, Albuquerque G. Advantages and Limitations of Electro-Mechanical Finishing, The Santa Fe Symposium on Jewelry Manufacturing Technology 2009, 2009.
[23] Zeilmann, R. P., & Machining Group (GUS), University of Caxias do Sul. (2024). Tribological Conditions Between Tool and Workpiece for Polished Tools: Final Report 2021–2024. University of Caxias do Sul (UCS)
[24] Denkena, B., & Biermann, D. Cutting edge geometries. CIRP Annals, 63(2), 631–653., 2014
[25] Wang, W., et al. Effect of edge preparation technologies on cutting edge properties and tool performance. Int. J. Adv. Manuf. Technol., 105, 1823–1838, 2019.