INDUSTRIE AUTOMOBILE
Moins de frottements – moins de CO2 – plus de performances!
Dans l’industrie automobile comme dans le domaine de la compétition, les surfaces à frottement optimisé du moteur et de la chaîne cinématique réduisent les frottements et l’usure des matériaux. Les structures de surface lissées et isotropes réduisent les émissions de CO2 et augmentent la durée de vie des composants. Avec l’utilisation d’huiles de plus en plus peu visqueuses, les surfaces des composants sont soumises à des exigences élevées. Même des tâches prétendument simples, comme l’ébavurage ou le rayonnage ciblé, entraînent une charge de travail importante au stade de la production. Les procédés développés individuellement par OTEC permettent d’enchaîner les étapes de process entre elles afin d’augmenter les performances, de réduire les émissions et de simplifier la fabrication.
Pour en savoir plus sur les mavantages mesurables du traitement de surface ciblé OTEC, lisez l’interview de Florian Reinle, ingénieur R&D chez OTEC.
ANALYSE COMPARÉE DES PROCÉDÉS – LA TRIBOFINITION VIBRANTE OTEC SÉDUIT
Traditionnellement, on utilise en traitement de reprise la finition par bande, la rectification par polissage ou même des procédés accélérés par voie chimique. Par rapport au ponçage vibrant avec les systèmes OTEC, la finition par bandes est coûteuse en bandes et entraîne des temps de préparation longs. De plus, la structure de surface obtenue est directionnelle (non isotrope).
Le traitement accéléré par voie chimique, par exemple dans un vibrateur linéaire, utilise des produits chimiques classés comme particulièrement préoccupants, tels que le chromate (de sodium) et l’acide chromique. En outre, l’approvisionnement, la neutralisation et l’élimination entraînent des coûts élevés, ce qui réduit la rentabilité économique du traitement de reprise. Les systèmes de tribofinition d’OTEC utilisent un traitement exclusivement mécanique. Ils obtiennent ainsi les meilleurs résultats dans les plus brefs délais pour les pièces en vrac et les pièces isolées.
Les technologies OTEC sont particulièrement intéressantes pour
- Surfaces à frottement optimisé (p. ex. les pièces de transmission dans les groupes motopropulseurs électrifiés)
- En combinaison avec le grenaillage de précontrainte (lissage des engrenages après sablage)
- Application de contraintes résiduelles de compression directement à la périphérie
- Réduction de l’usure grâce à l’augmentation de la portance des piqûres et à la réduction des micropiqûres
- Utilisation de lubrifiants à faible viscosité ou à base d’eau
- Combinaison de plusieurs étapes de process, p. ex. lissage et ébavurage en une seule étape
- Prétraitement et post-traitement des revêtements anti-usure
PRODUCTION EN LIGNE AVEC OTEC
Les machines de polissage à flux continu sont adaptées au traitement d’un grand nombre de pièces en série grâce au chargement automatique des pièces. La conception modulaire permet de configurer les machines en fonction de la tâche de traitement visée.
ÉLECTROMOBILITÉ
Face aux bouleversements structurels que connaît l’industrie automobile, OTEC apporte une contribution positive dans le domaine de l’électromobilité. La connectivité et l’électrification sont en effet au cœur des préoccupations de l’industrie automobile mondiale.
Dans la transmission d’un groupe motopropulseur électrique, une grande partie de la puissance est convertie via la denture. Avec les méthodes de traitement de surface conventionnelles, la finition de surface est souvent plus grossière, ce qui limite le potentiel d’amélioration de l’efficience.
Avec notre procédé de polissage à flux continu, c’est précisément à ce niveau que nous intervenons afin de pouvoir exploiter pleinement ce potentiel. Les pertes par frottement sont réduites lors du traitement de surface des pignons. Par conséquent, l’efficience augmente et l’empreinte carbone du client final diminue. L’aspect environnemental est un défi central. C’est pourquoi OTEC mise également sur des méthodes de tribofinition respectueuses de l’environnement pour le fonctionnement de ses installations.
Les équipementiers et les fabricants de transmissions obtiennent ainsi une plus grande autonomie dans l’application ultérieure, avec une consommation plus faible et moins d’émissions. Le procédé de polissage à flux continu a donc un effet positif direct dans l’application. L’efficience accrue permet d’obtenir une plus grande autonomie avec la même taille de batterie.
Applications pour la vis de direction : grincements des freins, gémissements de la transmission, embrayage qui patine. Afin de minimiser les vibrations audibles et perceptibles dans les véhicules automobiles, qui sont désignées par le terme NVH (Noise, Vibration, Harshness), OTEC traite les composants des boîtiers de direction, tels que les vis de direction, avec le procédé éprouvé du polissage à flux continu. Les irrégularités, qui entraînent par exemple des coefficients de frottement plus élevés sur un flanc, sont ainsi éliminées.
pplications pour l’arbre du rotor : pour le joint d'arbre radial grande vitesse, l’interface entre la surface de contact du joint et la lèvre d’étanchéité est soumise à des exigences très élevées. Dans certains cas, les performances doivent donc être améliorées. Si la surface de contact est lissée à l’aide du procédé du polissage à flux continu, il est possible d’augmenter la durée de vie du système d’étanchéité soumis à la contrainte élevée de la vitesse de glissement.
Application moteur électrique : Les stators de type hairpin sont souvent utilisés dans les moteurs électriques. Ces hairpins (ou épingles à cheveux) sont composées d’un fil de cuivre recouvert d’un isolant. Lors de la fabrication automatique et du montage des hairpins, une manipulation extrêmement soigneuse est nécessaire, afin de protéger l’isolation de tout dommage. Toutes les pièces de l’installation de fabrication qui entrent en contact avec le fil doivent par conséquent être finement ébavurées et polies.
Les machines OTEC et leurs processus garantissent l’arrondi des bords d’outils et des autres pièces en contact avec le fil, ainsi que le polissage parfait des surfaces. La géométrie des outils n’a ici aucune influence.
Il est possible de lisser et de polir sans problème les outils suivants :
• Rouleaux de décintrage
• Rouleaux de pliage
• Poinçon de découpage
• Outils de formage et matrices
• Poinçon de cintrage
• Outils de croisage
• Préhenseur
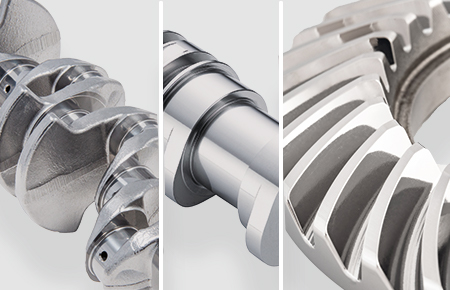
LISSAGE | POLISSAGE
Exemples d’application :
pièces de came, vilebrequin, composantes de boîte de vitesses, engrenages de différentiel / engrenages hypoïdes, bielles, pièces de direction, axe de direction, actionneursEn savoir plus
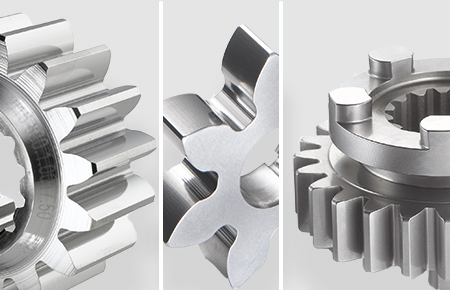
ÉBAVURAGE | RAYONNAGE
Exemples d’application :
rondelles de réglage d’huile (shims) dans les amortisseurs, roues dentées, roues de chaîneEn savoir plus
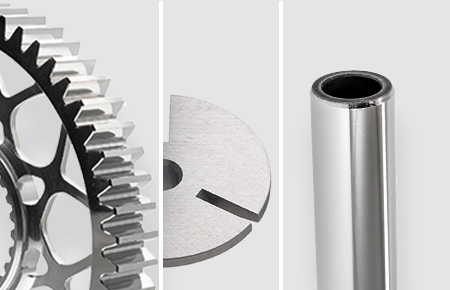
Autres applications
Exemples d’application :
impression 3D, compétition (soupapes, pièces de boîte de vitesses, vilebrequin, pistons, segments de piston…), entraînements électriques, structure de surface isotrope, pied de bielleEn savoir plus