AUTOMOTIVE INDUSTRY
Less friction – less CO2 – improved performance!
In the automotive industry and in motor racing, friction-optimised surfaces in the engine and drivetrain reduce friction and wear. Smoothed and isotropic surface structures reduce CO2 emissions and increase the service life of components. The use of increasingly lower viscosity oils presents huge challenges for the component surfaces. Even supposedly easy processing tasks such as deburring or targeted edge rounding often involve a lot of time and effort during manufacture. Custom-developed OTEC processes can be used to interlink process steps, improve performance, reduce emissions and make production easier.
To learn more about the measurable benefits of targeted OTEC surface processing, listen to the interview with Florian Reinle, R&D engineer at OTEC.
PROCESS COMPARISON – OTEC MASS FINISHING IS IMPRESSIVE
Belt finishing, polish grinding or even chemically accelerated processes are conventionally used during finishing. Compared with mass finishing using OTEC machines, belt finishing involves high costs for finishing belts and long set-up times. In addition, the resultant surface structure is directional (not isotropic).
Chemically accelerated processing as in trough vibrators, for example, uses chemicals such as (sodium) chromate and chromic acid, which have been classed as substances of very high concern. They also involve high costs for procurement, neutralisation and disposal, which make finishing less cost effective. OTEC mass finishing machines use only mechanical processing during the finishing process. This gives the best results in the shortest time for bulk materials and piece goods.
OTEC technologies offer particular advantages for
- Friction-optimised surfaces (e.g. transmission in electric drivetrains)
- In combination with shot peening (smoothing of gears after peening)
- Introduction of compressive residual stress directly in the edge zone
- Reduced wear by increasing pitting resistance and reducing micropitting
- The use of low-viscosity or water-based lubricants
- Combination of several process steps, e.g. smoothing and deburring, in one step
- Pre- and post-treatment of wear-resistant layers
LINE PRODUCTION WITH OTEC
The stream finishing machines with automatic workpiece loading are ideal for processing large quantities in series production. The modular design allows a configuration of the machines that is tailored to the specific processing task.
E-MOBILITY
In the face of structural upheavals, OTEC is making a positive contribution in the area of e-mobility. The global automotive industry is focussed mainly on connectivity and electrification.
A lot of power is converted via the gearing in the gearbox of an electric drivetrain. With conventional surface processing, the surface finish is often rougher, and the potential for increasing efficiency is limited.
With our stream finishing process, we start exactly at this point and exploit the potential to the fullest. Friction losses are reduced during surface processing of the gears. This increases efficiency and reduces the CO2 footprint of the end customer. The environmental aspect is a central challenge, which is why OTEC also relies on environmentally friendly mass finishing methods for operating the machines.
OEMs and gearbox manufacturers produce fewer emissions and thus achieve higher ranges with less consumption during subsequent use. Stream finishing thus offers a direct benefit in actual use. A longer range can be achieved through increased efficiency with the same battery size.
Steering worm applications: Squeaking brakes, gear whine, juddering clutch. To minimise audible and perceptible vibrations in motor vehicles - Noise, Vibration, Harshness (NVH), OTEC processes components of steering gears such as steering worms using proven stream finishing. Uneven surfaces, which result in higher friction values on edges for example, are thus smoothed.
Rotor shaft applications: On radial shaft high-speed seals, the interface between the seal running surface and the sealing lip is subject to the highest demands. In some cases, the performance must therefore be increased. By smoothing the running surface using stream finishing, it is possible to increase the service life of the sealing system under the high sliding speed load.
Application electric motor: Hairpin stators are often used in electric motors. The hairpins are made of copper wire that is insulated with a coating. During automated manufacturing and assembly, it is crucial that hairpins are handled carefully to avoid damaging the insulation. This means that all parts of the production system which come into contact with the wire must be superfinished with extremely fine deburring and mirror-polishing.
Regardless of tool geometry, OTEC machines and processes ensure that the edges of tools and other parts which come into contact with wire are rounded, and their surfaces perfectly polished.
Our machines can smooth and polish the following tools with ease:
• Straightening rollers
• Bending rollers
• Cutting punches
• Forming tools and dies
• Bending punches
• Setting tools
• Handling grippers
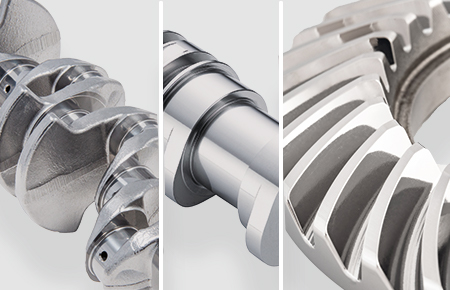
SMOOTHING | POLISHING
Application examples:
Cam pieces, crankshaft, transmission parts, differential/hypoid gears, connecting rods, steering parts, steering gear spindles, actuatorsMore information
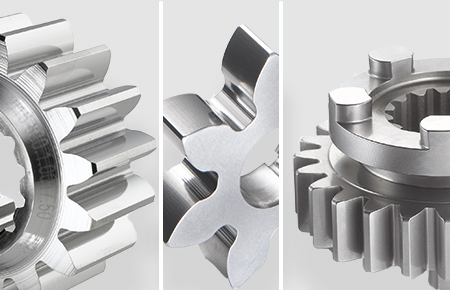
DEBURRING | EDGE ROUNDING
Application examples:
Oil control shims in shock absorbers, gearwheels, sprocketsMore information
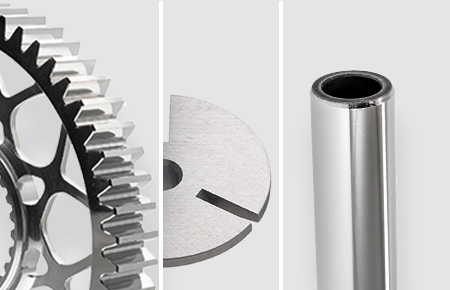
Other applications
Application examples:
3D printing, racing (valves, transmission parts, crankshaft, pistons, piston rings, ...) E-drives, isotropic surface structure, piston pinsMore information