OTEC NEWS
press releases
Alongside company news you'll find solutions to some intriguing and tricky surface technology issues – simple concise, practical advice on deburring, grinding, smoothing and polishing.
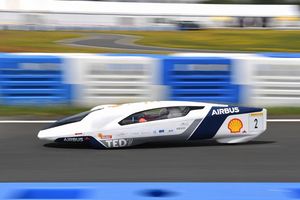
12/20: shell eco-marathon
OTEC Präzisionsfinish puts AIRUS-Team TED in pole position
The Shell Eco-marathon is one of the biggest energy efficiency competitions in the world. The challenge is to design a vehicle that can travel further than any other on just one litre of fuel. Drivetrain friction plays a huge part in this. AIRBUS’s team TED (Technologies et Energies de Demain) has the advantage of OTEC Präzisionsfinish know-how: targeted surface processing technology that produces a marked improvement in the tribological properties of drive components.
more...
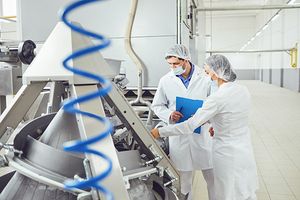
12/20: OTEC mass finishing Solutions for the food industry
Food production systems: automated surface smoothing for components
Cast, milled and turned machine components for food production have rough surfaces and sharp, unhoned edges. This not only leaves products prone to food residues and micro-organisms as well as contamination by small fragments from unstable component edges, but also results in high levels of component wear and therefore shorter service life. Efficient mechanical surface processing eliminates these problems.
more...
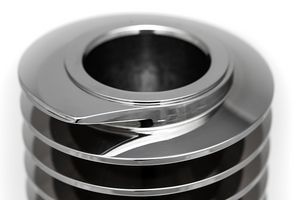
12/20: Food Industry - Extruder screws perform better with evenly smoothed surfaces
Schaaf Technologie GmbH relies on OTEC stream finishing process
Schaaf Technologie GmbH manufactures screw extruders. Manually post processing the parts after turning and milling used to take the company around four hours. With the stream finishig process manual finishing is a thing of the past.
more...

12/20: COIN PRODUCTION TOOLS
COIN HUBS AND DIE BLANKS: repeatable precision grindng and polishing
OTEC Präzisionsfinish drag finishing machines provide repeatable precision surface processing at two quality-related points in the process of turning metal into mint. In specific terms: mechanical, repeatable surface smoothing and polishing of the die blank, and of the hub produced from it after laser engraving. more...
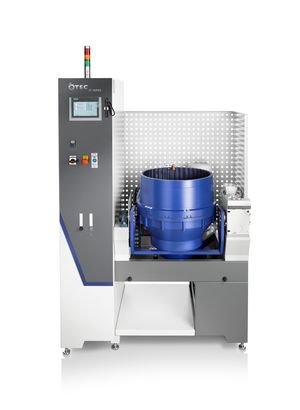
11/20: OTEC CF-SERIES
THE NEW DESIGN OF THE CF 50 DISC FINISHING MACHINE
The OTEC CF 50 disc finishing machine in the CF-Series now boasts a brand new design. Compact, it has an optimised welded structure that guarantees reliable operation and a long service life. It also features storage space for two compound containers and a waste water pumping station with a tray. The optimised spraying system with additional rinsing nozzle enables process containers with the patented zero gap system to be filled quickly.
more..
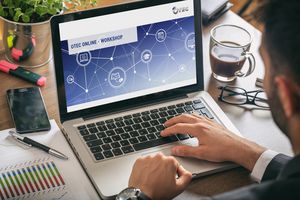
07/20: OTEC initiates online-workshops
Expert knowledge, tips and know-how about mass finishing
Helmut Gegenheimer, Managing Director of OTEC, summed up the situation: “The coronavirus has been a challenge for us. We had to find a replacement for trade fairs, customer visits and in-house mass finishing workshops at short notice. We devoted a lot of energy to getting OTEC’s online work-shops up and running overnight. Participants benefit from expert knowledge, tips and know-how about mass finishing that they can put to immediate use. more...
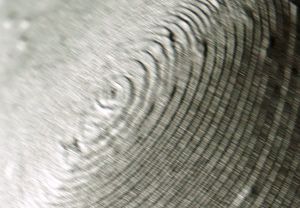
07/20: ADDITIVE MANUFACTURING:HOMOGENISED SURFACES FOR 3D PRINTED PARTS
OBTAIN THE PERFECT FINISH ON ADDITIVELY MANUFACTURED WORK-PIECES, WITH DISC FINISHING!
The greater the possibilities of this generative process, the higher the workpiece specifications be-come. Series quality is the name of the game, which means that surface quality, repeatability and process reliability are under the post-processing spotlight. more..
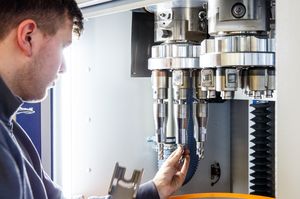
07/20: toolmaking industry
Rounded edges, reliable processes, less wear: mass finishing is a winner for Wunschmann precision tools
In drag finishing (or mass finishing), parts – in Wunschmann’s case milling tools for metal cutting – are pulled through a bulk container. The material abrasion is clearly specified beforehand: debur-ring/rounding or smoothing/polishing. This optimises the tool’s surface and improves its functional properties. more...
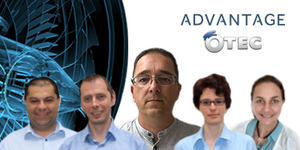
04/20: OTEC informs
reliable Partner Advantage is new Distributor for hungary
Since april is our long-time trusted Partner Advantage-fl.cz s.r.o., exklusive OTEC Distributor for hungary.
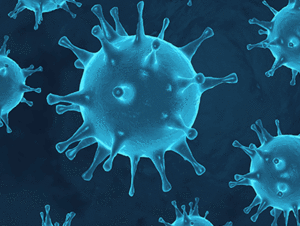
04/20: OTEC informs
Situation within Corona crisis
Information of the management on availability and business operations.
more...
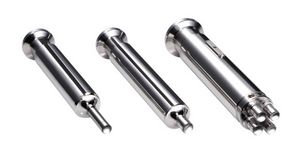
04/20: Stay up and running: tablet Tools with flawless surfaces
Automatic polishing saves time and money
A smooth pressing surface reduces friction between the punch and the powder, often increasing production rates as a result. It also reduces the tendency for tablets to stick, and therefore quite literally guarantees smoother processing. Polishing can significantly extend tool life as well as reducing the cost of replacement dies and machine downtime..
more...
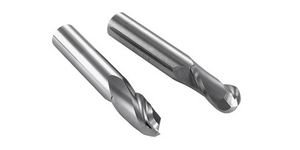
03/20: ONE process fits all?
Why custom processes for edge rounding on carbide tools are vital
Edge rounding (honing) on carbide tools is an established process that extends tool life and im-proves PVD coating adhesion. Rounding and smoothing the cutting edges minimises the risk of mi-crobreakage and significantly increases their mechanical stability. That’s the objective. Clear and simple.
more...
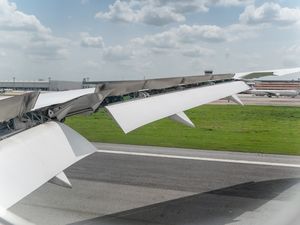
03/20: OTEC STREAM FINISHING OPTIMISES SERVO VALVES IN 40 SECONDS
BOOSTING EFFICIENCY: OTEC MEETS THE DEMANDING REQUIREMENTS OF AIRCRAFT CONTROL TECHNOLOGY
Precision deburring and smoothing of roughness peaks along with defined edge rounding on bushings and spools not only reduces friction in the valve but also increases its contact ratio. High-precision processing also enables the closest possible tolerances – a critical factor in system tightness. It also permits a higher switching or stroke frequency, significantly increasing control accuracy.
more...
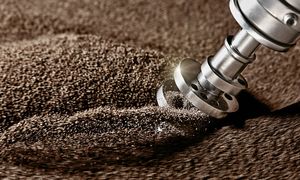
03/20: Automotive: Targeted Surface processing has measurable benefits
Interview
No doubt you’ve seen in the press that the EU plans to introduce automotive industry fines this year. Manufacturers will have to pay Brussels €95 for every newly licensed combustion engine vehicle that exceeds the CO2 threshold of 95 g/km. According to the Council on Clean Transportation, aver-age emissions in 2018 were 121 g/km.
Florian Reinle, an R&D engineer at mechanical engineering company OTEC Präzisionsfinish, high-lights how vehicle manufacturers can optimise their production processes and reduce friction at the same time.
more...