Rounded edges, reliable processes, less wear: mass finishing is a winner for Wunschmann precision tools
Germany-based manufacturer Wunschmann is boosting the performance of its precision cutters with OTEC’s new drag finishing machine.
“Actually, it goes completely against common sense,” laughs Stephan Wunschmann, “first we grind the cutting edges of our milling tools until they’re as defined as possible and then we round them off again in the drag finishing machine.”
It may sound like nonsense but there’s method in the madness: In drag finishing (or mass finishing), parts – in Wunschmann’s case milling tools for metal cutting – are pulled through a bulk container. The material abrasion is clearly specified beforehand: deburring/rounding or smoothing/polishing. This optimises the tool’s surface and improves its functional properties. The process on the OTEC DF-3 drag finishing machine takes between 30 and 60 minutes. Wunschmann GmbH has now been using the machine for several months at its Hailfingen site and is impressed with the results:
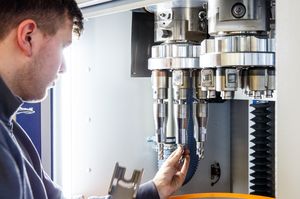
(Image source: KRAAS & LACHMANN Werbeagentur GmbH, Tübingen)
“A lot of our customers are sceptical about mass finishing at first, but it’s definitely won me over. Obviously it’s not suitable for every tool. You have to use it for specific purposes and always with accurately defined edge-rounding values. So you need to be prepared to tinker a bit to obtain the optimum rounding value for each cutter,” says Wunschmann, a toolmaking specialist and veteran, who invested almost €80,000 in the drag finishing machine.
Bite and wear resistance
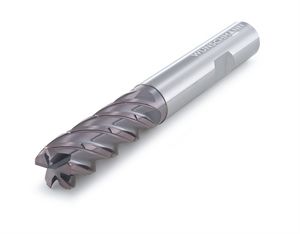
(Image source: KRAAS & LACHMANN Werbeagentur GmbH, Tübingen)
For example, preparing the edges in this way has extended the service life of the Wunschmann HPC-Vplus 187 high-performance cutter by around 30 percent when milling chromium-nickel steel (1.4301).
“The tool still bites despite rounding, and on top of that we’ve seen an improvement in wear re-sistance and process reliability,” says Wunschmann. “Before treating them, the cutting edges on our 187 were more ragged, which tended to cause erratic wear. Rounded edges wear more slowly and evenly.” Moreover, Wunschmann’s toolmaking experts have found that the benefits of mass finish-ing go beyond edge rounding: it also helps to polish chip flutes on milling tools, which in turn im-proves cutting performance and chip removal. All in all, Stephan Wunschmann considers the machine a good investment and believes that drag finishing will provide his customers with even higher-performance cutting tools. And not just new ones: edge rounding or chip flute polishing can also boost the performance of resharpened tools.
About Wunschmann GmbH
Wunschmann precision cutting tools have enjoyed a good reputation in metalworking for 40 years. Our customers rely on the quality and performance of our standard and custom tools made of solid carbide (SC) and high-speed steel (HSS). Long-standing users of our products value our technical expertise, experience and personal service.
OTEC drag finishing machines: quick overview
In drag finishing, the workpieces to be processed are secured in special holders. These are dragged through a container of grinding or polishing granulate in a circular motion at high speed. The quick motion generates a high pressure between the workpiece and the abrasive. This quickly leads to an optimum processing result in the form of precisely rounded edges, smoothing or a high-gloss finish in hand-polished quality.