OTEC News
Press releases
Alongside company news you'll find solutions to some intriguing and tricky surface technology issues – simple concise, practical advice on deburring, grinding, smoothing and polishing.
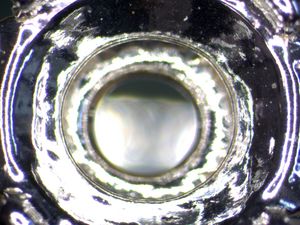
12/19: Nothing makes jewellery sparkle lika a uniform surface
OTEC's Disc finishing and electropolishing duo
Manual surface processing is particularly common in the jewellery sector. But it’s time-consuming, and time is money. One of OTEC’s international customers discovered to their great satisfaction that our two-stage mechanical process works like a charm on real silver jewellery.
more...
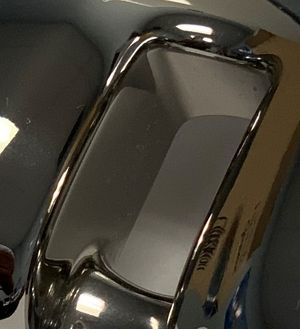
12/19: Stabilised Knee implants: targeted precision grinding & polishing with stream finishing
With accurray down the last micron, Surface Problems on stabilised knee implants are a Thing of the past
Knee prostheses come in various forms, but for patients with unstable ligaments or bone loss, doc-tors use the stabilised type, also known as axially supported. The two components (the femoral im-plant and the metal platform) are joined by a stabilising hinge. The functional feature of these prostheses is a “box” with inner geometry (see image, left). And therein lies the mechanical processing challenge, because conventional techniques quite literally can't hit the target.
more...
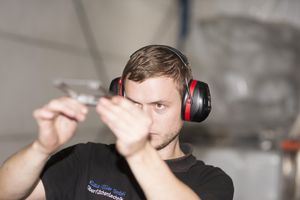
11/19: Partners in Innovation & Tradition since 1996
Klaus Müller GmbH and OTEC Präzisionsfinish
Neuenbürg-based grinding and polishing company Klaus Müller has especially close ties with OTEC Präzisionsfinish. We began discussions in 1996, with the added benefit that our businesses were only a few miles apart. OTEC – which at the time was what we’d now call a startup – was in search of the right compounds for its process development. Klaus Müller had exactly what we were looking for – and still does today. He and OTEC MD Helmut Gegenheimer struck up a partnership that has flourished ever since.In an interview with Klaus’ son, Boris Müller, we discover the key to this successful long-term relationship.
more...
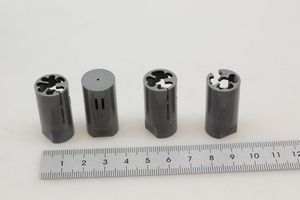
11/19: More security in space
Otec supports Tests for the roduction of new metals
Yes, that is true! Ceramic parts from CeramTec GmbH processed with OTEC precision finish fly around the earth in space - in a manned space station! How did this happen? The starting point was a research project: as the production of absolutely homogeneous metals on Earth is not possible - the production is subject to physical limits such as gravity - test series were carried out on board the space station, because certain physical limits simply do not apply in space. Here, metal can be melted without contact simply by bringing in energy in limited areas.
more...
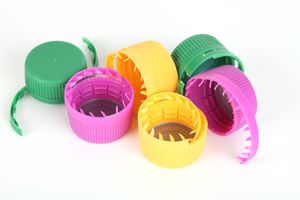
11/19: Screw Caps for bottles
High Efficiency and process reliability with polished moulds
The special moulds used for screw caps are usually turned from steel and then milled or injection moulded. In one mechanical post-processing stage (or two depending on the application), the mould is smoothed and polished so that the plastic caps produced on it will separate without sticking or residues, and without affecting the cap geometry. So the smoother the surface, the longer the mould provides top performance.
more...
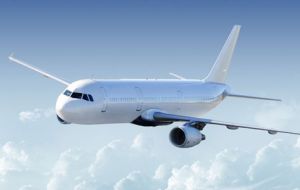
10/19: Aerospace specialist IFT opts for an OTEC finish:
Quality & accurary in the manufacture of high-precision parts
The exacting safety, precision and quality standards of the aerospace industry are as stringent as it gets. Every single manufacturing step has to be closely monitored and documented. Not every production facility can meet these multi-level requirements. OTEC customer IFT GmbH & Co. KG, based some 30 miles south of Frankfurt in Ober-Ramstadt, specialises in high-precision parts for the motorsport, medical technology and aerospace industries.
more...
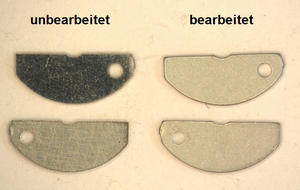
10/19: The Special requirements of lasercut parts
Precise, effektive Surface processing
Laser cut parts are used in many industries, from jewellery to automotive, electrical and optical engi-neering. Once manufactured, their edges are slightly burred, and the parts often suffer from unsightly discolouration. Much of the time, these defects are removed by hand, which is time-consuming and costly. The challenge is almost always the same: how to deburr and polish extremely thin parts – i.e. less than 0.4 mm thick and usually made of stainless steel – without changing their geometry. But also, during processing, how to prevent the parts from chafing against each other, or from getting wedged in the container or stuck in the gap.
more...
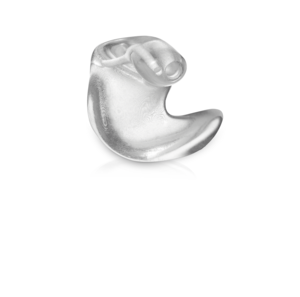
09/19: Surface Treatment for otoplastics
Best Fitting accuray with otec Precisionfinish
A gentle and effective surface treatment is necessary to prevent the otoplastics from being damaged during post-treatment and to maintain the geometry precisely. Often it is not possible to do completely without manual processing as a preliminary stage for mechanical post-treatment, because internal geometries are sometimes difficult to achieve with automated processes. Effective machining in the OTEC disc finishing machine reduces manual pre- or post-machining to an absolute minimum. This saves time!
Depending on the number of parts and the initial condition, it is possible to vary between different machines, process equipment and running times.
more ...
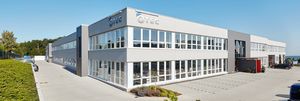
09/19: "Growth through innovation":
from Startup to mediumsized Technology leader (Interview with OTEC Founder)
The company was founded in 1996 by Helmut Gegenheimer and Soran Jota in Straubenhardt, near Pforzheim in the Southern German state of Baden-Württemberg. Since then, as a specialist in surface processing, it has grown from a mechanical engineering startup serving the jewellery and watchmaking industry to a global technology leader in deburring, grinding, smoothing and polishing. Today, international customers from industries as diverse as jewellery and watchmaking, medical devices, pharmaceuticals, automotive and aerospace, electronics, toolmaking and additive manufacturing rely on the expertise we’ve acquired over the course of more than twenty years. Here's an insight into the OTEC Story, with CEO Helmut Gegenheimer.
more…
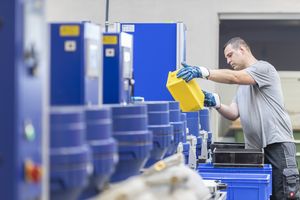
09/19: Quality creates STRong bonds
Dörfler & Schmidt and OTec Präzisionsfinish
Dörfler & Schmidt Präzisionsfinish and OTEC Präzisionsfinish are based about 140 miles apart – but it’s what bonds them that matters: a passion for precision finishing and a working relationship spanning two decades.
Felix Dörfler tells us why OTEC is the go-to machine manufacturer for service providers in surface processing.
more...
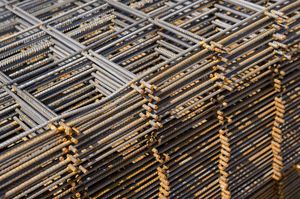
08/2019: Roll Forming parts:
A BETTER SURFACE = TOP QUALITY TOOLS = OPTIMISED TOOL SERVICE LIFE!
Forming rollers are used in applications like the manufacture of reinforcement mesh. The typical structure required is formed using appropriate machinery and dies. Our Italian customer also sup-plies its customers with the associated forming dies for notching, chamfering and marking, made from either reinforced steel or hard metals.
more...
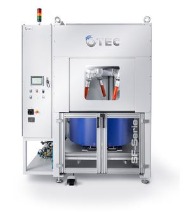
07/2019: Precise Surface Processing of PCD-Tools
report About UC Tools & OTEC
OTEC has developed a custom surface polishing process for UC Tools’ PCD range (PCD is an ultra-hard synthetic cutting material made from sintered diamond particles). The result: tools polished to perfection.
more...
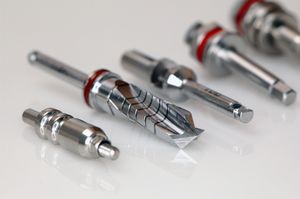
07/2019: Dental Drills:
OTEC PRODUCES OUTSTANDING RESULTS IN 60 SECONDS
The manufacturing process for stainless steel surgical drills used in minor or major procedures produces burrs. Manual deburring is not just time-consuming but also produces a lot of rejects, not to mention the fact that every drill ends up slightly different. It’s an unreliable process. OTEC SF Series machines are designed for reliable, reproducible precision processing. Drills pose specific challenges.
more...
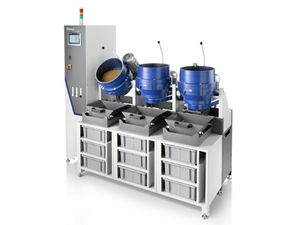
06/2019: new Design
OTEC DISC FINISHING MACHINE – REDESIGNED AND EVEN MORE REMARKABLE
The new design of the OTEC CF Series disc finishing machine is sure to impress. Modular and compact, it has an optimised welded structure that guarantees trouble-free operation and a long service life. more...
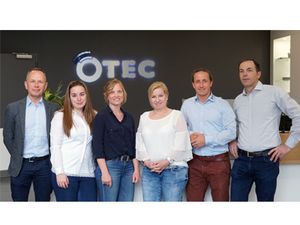
05/2019: OTEC in Switzerland
OTEC repositioned - close, competent and reliable
An experienced sales team of German, Italian and French speakers is waiting to assist you, expertly supported by the OTEC Service department, a new logistics centre and reliable local service partners. more...
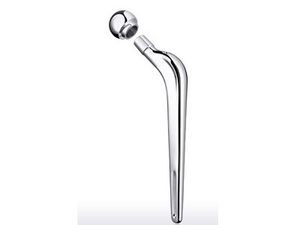
03/2019: PROSTHETIC HIPS
PERFECT SURFACE FINISHING WITH THE OTEC DRAG FINISHING MACHINE
The DF machine from OTEC ensures the correct combination of abrasive, tool holder and process parameters for a surface finish that is on a par with hand-finished quality. To guarantee these results, OTEC supports its customers by using its long years of expertise to develop customised processes.
more...
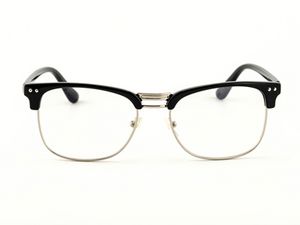
02/2019: Parts for glasses
A unique zero gap system for damage-free processing
Glasses are mainly worn as an optical aid to correct defective vision and misalignment, in which case they are also referred to as corrective glasses. The parts for glasses have to be deburred, rounded and highly polished. Due to OTEC's unique zero gap system, small metallic parts for glasses can processed without damaging and get a flawless, highly polished surface.
more...