The manufacturing process for stainless steel surgical drills used in minor or major procedures pro-duces burrs. Manual deburring is not just time-consuming but also produces a lot of rejects, not to mention the fact that every drill ends up slightly different. It’s an unreliable process. OTEC SF Series machines are designed for reliable, reproducible precision processing. Drills pose specific challenges.
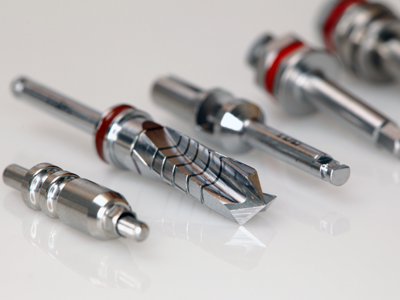
To guarantee their best performance in patient care, it’s essential that the cutting edges are not too rounded. To prevent bone-cell damage and stop metal residues from entering wounds, it’s also criti-cal that the edges are sharp, but free of burrs. At the same time, the surface must be smooth enough to ensure no tissue or blood adheres to the drill. And after use, surface finish is a decisive quality factor in easy, effective cleaning and maintenance.
Astonishingly fast mass finishing
Italian manufacturer uses a pulse finish process on the OTEC SF-1 ILS to guarantee the quality of its high-grade bone and dental drills. During process development, our pulse finish produced outstand-ing results in just 60 seconds. That’s an output of 40 units per hour. The machine runs for up to five hours without the need for an operator.
Perfectly coordinated parameters and abrasives provide our customer with consistent, reproducible results. The machine’s high processing forces and flow rates cut processing times, making it extremely cost-efficient. What’s more, the automated loading system on the SF Series is ideal for increasing throughput as well as for integration in a production line.
Video of SF ILS with chain loader (YOUTUBE) >>