OTEC News
Press releases
Alongside company news you'll find solutions to some intriguing and tricky surface technology issues – simple concise, practical advice on deburring, grinding, smoothing and polishing.
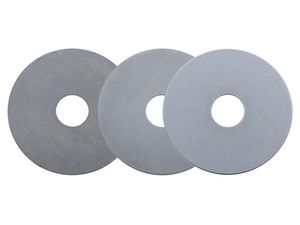
11/2017: Shock absorber discs
EFFECTIVE DEBURRING, ROUNDING AND RELIABLE SEPARATION
Stamped parts are used in a wide variety of applications in the automotive industry and are used, for example, in shock absorbers. The main processing task is deburring and rounding of the edges. Due to the thickness of the components of less than 0.5 mm, some challenges arise during surface finishing. The OTEC disc finishing machines of the series CF allow that sensitive stamped parts will be deburred and rounded quickly, absolutely reliably and process capable. This can be 20 times more effective than conventional vibrators.
more...
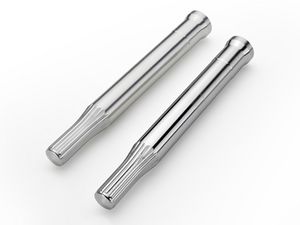
10/2017: INNER FORMING DIES FOR NON-CUTTING PRODUCTION
TOOLS IN TOP FORM
Depending on the process, inner forming dies are exposed to very high pressures combined with high sliding speeds. This means that very strenuous demands are placed on the tools and especially on the surfaces! With OTEC stream finishing machines tools can be processed economically and in consistent quality. The result is a perfectly polished forming tool with reduced friction coefficient and increased tool life.
more...
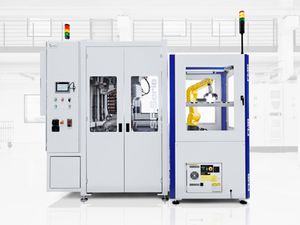
09/2017: NEW OTEC SOLUTIONS FOR THE TOOL INDUSTRY
AUTOMATIC EFFICIENCY
OTEC offers high-performance machines for drag and stream finishing, specially tailored to the needs of the tool industry. Combined with customised OTEC process parameters, these machines can process cutting, forming and injection moulding tools at low cost.
more...
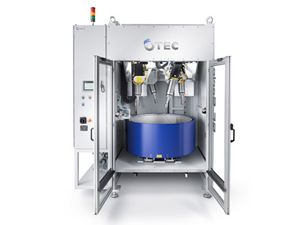
08/2017: SURFACE FINISHING IN THE AEROSPACE INDUSTRY
EXTREME CONDITIONS CALL FOR PERFECT RESULTS
OTEC machine technology opens up new possibilities for the finishing of components in the aerospace industry. For the first time ever, perfect machine finishing of surfaces is a reality – with high-precision results and a more consistent quality than can be achieved by hand. Turbine blades, gear wheels und blisks can be deburred, rounded and smoothed in a single processing stage.
more...
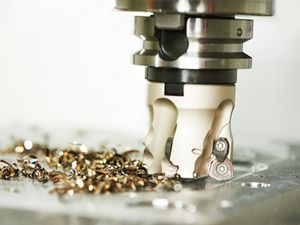
07/2017: TOOL BODIES
PERFECTLY DEBURRED AND POLISHED
For surface processing, two main tasks are involved in the production of cutter bodies: Deburring after milling and polishing after hardening and grinding. The reliable removal of burrs is important for optimum fit of the inserts on the cutter body. A burr-free and flat support surface is important for stability during the cutting process and prevents chipping of the insert. The subsequent polish removes the oxide layer formed during hardening, thereby improving the visual appearance and upgrading of the part for sale.
more...
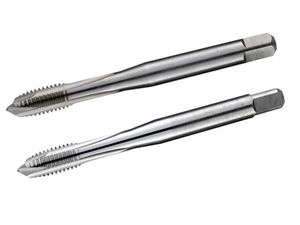
06/2017: SURFACE FINISHING OF THREADING TOOLS
DEBURRING, ROUNDING AND SMOOTHING with PULSFINISH
The requirements to the surface finishing of threading tools could be very different depending on the type of tool. Therefore a very flexible process that adapts to every dimension and shape of tools is necessary. In OTEC-stream finishing machines with pulse drive (Pulsfinish) the tools can be deburred, smoothed and rounded reliably, quickly and economically according to the requirements.By this finishing process, the cutting and deformation forces can be reduced by about 60%.
more...
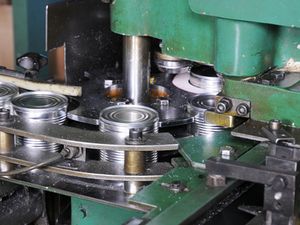
05/2017: POLISHING OF CAN SEAMERS
COST-EFFECTIVE FINISHING WITH PERFECT RESULTS
Can seamers are used to seal cans. The key functional surface of the tool is the forming surface or groove which joins together the edges of the can and the lid by forming a seam. Can seamers are used in large quantities all over the world.In order to ensure that the tools always maintain a consistent quality, the forming surfaces must be regularly repolished.
more...
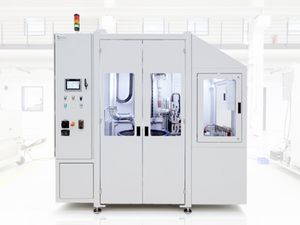
05/2017: EFFICIENT TOOL FINISHING WITH THE NEW SF1-AUTOMATION
NON-STOP PERFECTION
The quality of stamping, forming and cutting tools can be improved considerably by finishing in the DF and SF machines from OTEC. With the SF1 ILS with chain loader, OTEC sets a new standard in automated precision finishing. This machine is specially tailored to the requirements of the toolmaking industry and its automated loading system delivers clear cost benefits.
more...
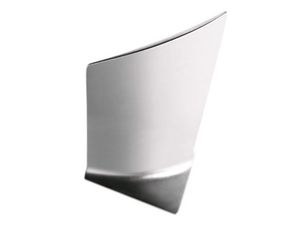
04/2017: SMOOTHING OF TURBINE BLADES
SELECTIVE SMOOTHING WITH STREAMFINISH
After manufacturing, all turbine blades require surface finishing before they can be used in an aircraft or for power generation, since either the initial roughness is too great or the edges are too sharp. Homogeneous smoothing of the surfaces and rounding the edges not too strongly is important. With OTEC stream finishing machine the edges could be rounded to a defined measurement.
more...
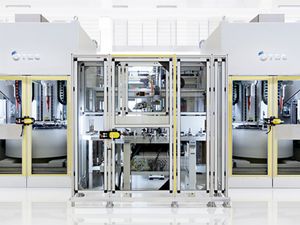
03/2017: STREAMFINISH FOR THE AUTOMOBILE MANUFACTURING
FULLY INTEGRATED INTO AUTOMOBILE MANUFACTURING
OTEC’s stream finishing and pulse finishing units have been specially tailored to the requirement profile of assembly line production in the automobile industry or high-tech tool industry, in order to meet the high standards of process reliability, speed and processing quality demanded by large-scale series production. This system type enables our customers to deburr, round and smooth camshafts simultaneously and in a very short time.
more
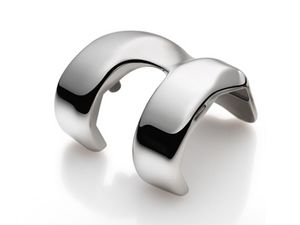
03/2017: SURFACE FINISHING FOR IMPLANTS
MIRROR FINISH FOR MEDICAL IMPLANTS
OTEC Präzisionsfinish GmbH has extended the range of applications for automated grinding and polishing processes to medical engineering. This means that a new dimension in surface finishing can be achieved during the manufacture of medical implants. Special parameters for the drag finishing and disc finishing processes make it possible to achieve fast and economical surface finishing combined with consistent quality for e.g. implants, ear moulds and bone screws.
more...
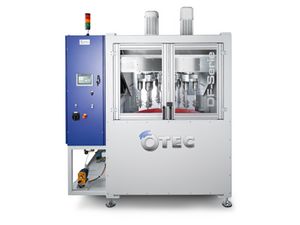
02/2017: MUCH MORE POWER AND SPACE - THE NEW DF-5/330 WET
FROM CUSTOMISED SOLUTION TO SERIES PRODUCTION MODEL
The customer’s requirements for finishing gear wheels presented a considerable challenge: a completely new machine concept for holding large and heavy workpieces needed to be developed. The result is the biggest and most powerful DF machine that OTEC has so far put on the market. The task was the deburring of gear wheels, whereby two gear wheels had to be held in each workpiece holder. It was also necessary to observe a maximum processing time of four minutes
more...
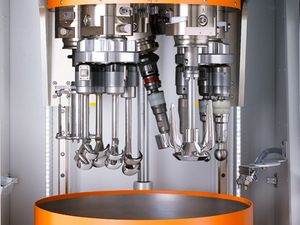
02/2017: POLISHING OF KNEE JOINTS
MASS FINISHING OF JOINT IMPLANTS
The contact surfaces of hip and knee implants must be homogeneous, precise and very smooth. In order to achieve this, OTEC has developed special mass finishing processes for drag finishing. Especially when treating the complex surface geometry of a knee joint, it is important for the material to be removed evenly during grinding and polishing, in order to ensure a perfect fit.
more...