SURFACE FINISH FOR medical IMPLANTS
Mirror finish for implants
Nothing lasts for ever – at least not in endoprosthetics. Even the very best quality of implant has only a limited life. One of the main factors in this is the quality of the surface finish. OTEC Präzisionsfinish GmbH has extended the range of applications for automated grinding and polishing processes to medical engineering. This means that a new dimension in surface finishing can be achieved during the manufacture of medical implants. Different types of implant place vastly differing requirements on the surface finish. Depending on the field of application, there are a number of criteria which determine the quality of the product: a highly accurate fit, a homogeneous surface, pronounced or minimal edge rounding. Combined with the complexity of the shapes normally involved, these factors have made reliable automated processing virtually impossible, until now.
Cost-effective and consistent quality
As a result of several years’ work, OTEC Präzisionsfinish GmbH has developed special parameters for the drag finishing and disc finishing processes to meet the particular requirements of implant manufacturing. This makes it possible to achieve fast and economical surface finishing combined with consistent quality. Workpieces of any shape and weight can be deburred, ground, smoothed and polished in a very short time. This is performed by moving the workpieces through a customised composition of abrasive media, whereby the workpieces themselves are either loose or fixed in a rotating holder.
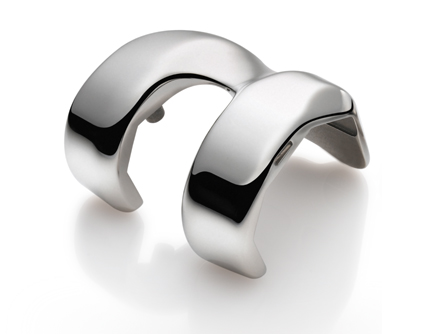
Joint replacements
In the case of hip or knee joints, a homogeneous, very smooth and highly polished surface is demanded of the contact areas. For this purpose OTEC has developed a special dry process for drag finishing. In this process the workpieces are clamped in suitable holders and dragged through the appropriate grinding and polishing media in a number of stages. Clamping the workpieces prevents them from damaging each other. The processing results depend on determining the ideal clamping angle. This enables Ra values of 0.03 μm to be achieved.
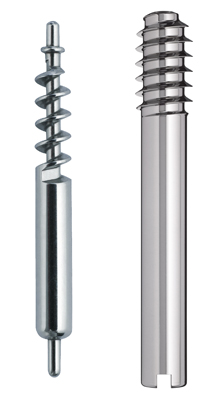
Bone screws and dental implants
Bone screws and dental implants are made of special stainless steel or titanium alloys. In order to obtain a good fit, unrounded but bur-free edges are required as far as possible. A smooth, polished surface is conducive to easy insertion and removal. Furthermore, the smooth surface simplifies the process of disinfection immediately before use. OTEC has developed a way to fulfil all three requirements in a single process. By using a disc finishing machine it is possible to create a smooth, highly polished surface without any significant edge rounding. After this single-stage process the workpieces are light in colour, have a pristine finish and exhibit a much higher quality. In this process Ra values of 0.03 μm can be attained.
Bone plates
In contrast to this, bone plates usually require a considerable degree of edge rounding and the surface should be as smooth and homogeneous as possible. Here, too, a disc finishing machine is used, albeit with different process parameters. This enables all traces of stamping and chip removal operations to be removed in a very short time and produces a smooth, high-quality surface.
Ear moulds
So-called otoplastic parts for hearing aids or hearing protectors are made from special plastics in a rapid manufacturing process. This manufacturing process creates a rough surface which does not provide the accurate fit and comfort required for insertion into the human ear. OTEC has developed a process with which the ear moulds can be ground in a disc finishing machine in a relatively short time. The special design of the machine gives a very high-quality smooth surface finish in a process that is gentle on the material. This means that sensitive workpieces can be processed very quickly and reliably without fear of damage, eliminating the need for complex and time-consuming manual polishing and the quality variations associated with manual processes.
From consultation to series production
In order to best fulfil the requirements of each individual application, it is essential to determine the ideal combination of all relevant process parameters. This includes amongst other things the choice of process, the composition of the processing media, the speed of rotation, the processing time and (in the case of drag finishing) the clamping angle.
For both processes OTEC supplies machines in a variety of sizes, from bench top units to fully-automatic plants. As for the choice of the right medium, potential customers are invited to have a sample of their product processed free of charge at OTEC’s finishing center. This service is available to customers all over the world. Systems for separating the finished workpieces from the processing medium and for reprocessing the water used complete the OTEC range of products.
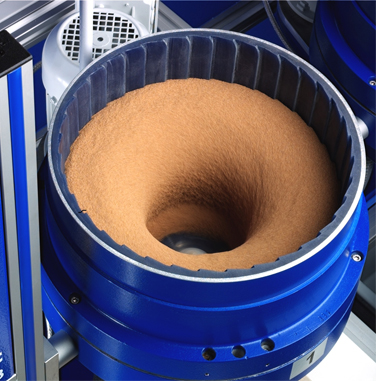