Smoothing of turbine blades
Selective smoothing with streamfinish
Turbine blades come in all shapes, sizes and materials. In some cases, turbine blades need to withstand extreme environmental conditions. In modern gas and aircraft turbine, combustion temperatures are often well over 1,000°C. This means that very strenuous demands are placed on the surfaces and materials used, as well as on the manufacturing and finishing processes.
The manufacture of turbine blades involves many different mechanical manufacturing processes. These include forging, milling, casting and increasingly also additive manufacturing processes such as 3D printing in laser sintering. Simply milling a single turbine blade on a five-axis machine takes at least about an hour. After manufacturing, all parts require surface finishing before they can be used in an aircraft or for power generation, since either the initial roughness is too great or the edges are too sharp. There are two tasks involved here:
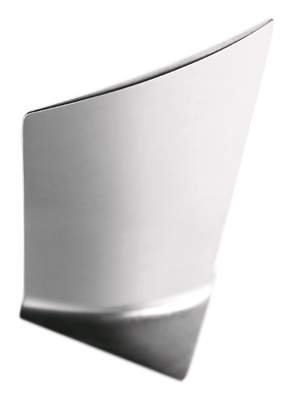
Homogeneous smoothing of the surfaces:
Generally to Ra < 0.4 μm, often even less than Ra 0.25 μm. Here, it is especially important not to unduly affect the contour of the blade.
Rounding the edges to a defined measurement:
Here it may be necessary to round the edges of the blade to different parameters. This rounding is traditionally carried out on CNC machines or done by hand. However, since the thickness of the blade may differ along the edge, this is no easy task. The main problem with this is that the blades might become too strongly rounded at the corners.
In the past, and for the most part still often today, smoothing has been carried out by hand. The main disadvantage of this, in addition to the high costs involved, is the fluctuation in the quality of the results. The use of robots for polishing reaches its limits as soon as the work-pieces take on a complex geometry, as is the case, for example, with blades made up of a number of guide vane segments.
In addition to the individual turbine blades, guide vane segments can also be smoothed. This can only be achieved with the stream finishing process. Here, the stream finishing process offers a first-class alternative. In this process, the turbine blades are immersed in a rotating drum filled with a process medium (an abrasive medium). The stream of process medium generated by the rotation of the drum acting in combination with the setting of the immersion angle produces a defined stream of medium acting on the surfaces to be finished. The direction and angle of contact can be precisely defined in order to optimize the finishing process to the specific geometry of the workpiece. Generally speaking, wet processes are used for this, which means that in addition to the process medium, an additive is used together with water to carry away the particles removed by abrasion. The most suitable media for this are lightly flowing abrasives which provide the most homogeneous media stream at the workpiece. OTEC manufactures a number of different versions of its stream finishing machines (SF machines) for the purpose of finishing turbine blades, and these can be customized and equipped to cater for specific requirements. Furthermore, the machines can be loaded and unloaded either manually or automatically by means of a standard robot cell.
Selective smoothing is possible
In addition to the option of automation, the machine offers the additional advantage that the selective direction of the process media stream ensures that neither the leading nor the trailing edges are rounded too strongly.
The blades are clamped in such a way that the corners are at the top during the finishing process and almost emerge from the process medium. The most commonly used medium is KM 6. During the process, the blade is directed toward the stream and swings to and fro at a predefined angle (e.g. +/- 30°) in order to achieve a homogeneous surface finish. Depending on the process medium used, the surfaces can reach roughness values of up to Ra 0.1 µm. Processing times are between two and thirty minutes. A higher output can be guaranteed by clamping up to five workpieces at a time in a single machine.
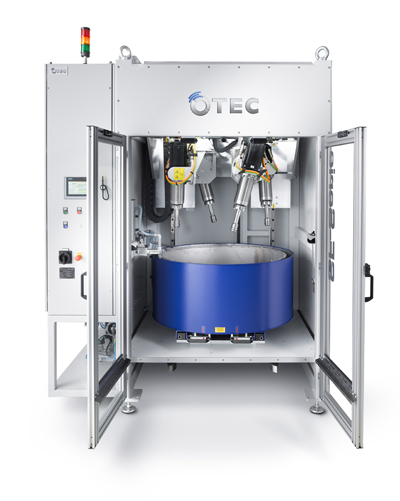