Automotive: Targeted surface processing has measurable benefits
Interview
No doubt you’ve seen in the press that the EU plans to introduce automotive industry fines this year. Manufacturers will have to pay Brussels €95 for every newly licensed combustion engine vehicle that exceeds the CO2 threshold of 95 g/km. According to the Council on Clean Transportation, average emissions in 2018 were 121 g/km.
Florian Reinle, an R&D engineer at mechanical engineering company OTEC Präzisionsfinish, highlights how vehicle manufacturers can optimise their production processes and reduce friction at the same time.
Florian, your work at OTEC is focused on friction, so you understand the pressure on the automotive industry. What do you recommend?
“We know from experience as well as talking to customers that targeted, application-optimised smoothing of friction contact surfaces makes a big difference in terms of efficiency. Sliding friction components like cam pieces, piston rings, crankshafts and gears can be mechanically smoothed with a high degree of precision. And smoothing has the added benefit of deburring, so we’re actually talking about an all-round improvement to the component.”
It seems like a complex subject. Can you explain what you mean by targeted surface smoothing?
“Sure! It means levelling the surface and removing roughness peaks and machining grooves to produce an isotropic surface, and an agreed roughness based on the customer’s requirements.
Our process actually employs high friction energy to prepare components for use in a way that reduces both surface friction and wear. The process produces a shear layer by changing the surface structure and creating compressive residual stress, which is highly effective in conditioning the component for use.
Taking that thought a step further, precision finishing reduces friction in the drivetrain, which means lower fuel consumption – i.e. more efficient use of drive power – and lower CO2 emissions.”
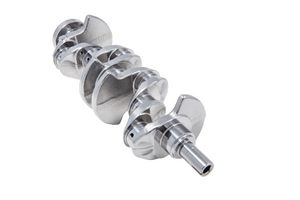
That sounds very promising – can you talk more specifically about the other advantages and explain how the process enhances the component generally?
“The mechanical processing per se delivers process reliability and repeatability in minimal time, so it increases cost effectiveness. But it also improves product quality – you can tell immediately just by looking at the component. If we then add deburring or targeted edge rounding to the equation, there are other tangible benefits because it obviously improves assembly handling in terms of pressing in parts or inserting delicate components like gaskets. It quite literally improves slip. Parts that are subject to heavy friction and wear are often coated. Optimising the surface beforehand improves adhesion and makes coatings more stable. Components can even be smoothed after coating.
The improvement in NVH behaviour is a particular bonus because it reduces audible or perceptible vibrations. And smoothing the surface has a synergistic effect that improves NVH behaviour above and beyond the component itself. For instance, it means you can use lowviscosity lubricants and boost the efficiency of the whole system.”
The press are saying that electromobility is the ultimate solution if vehicle manufacturers want to limit or avoid fines.
“Yes. Policies are promoting an ongoing increase in electric vehicles, and that affects the various vehicle classes to a different extent. Most reports concern the increase in electric drive production.
But production alone isn’t enough – the vehicles also have to sell. And that’s where competition and consumers come into play. End customers considering an electric car look carefully at the cost-benefit ratio, particularly in terms of range, purchase price and operating costs.”
Do friction and NVH play a role in e-mobility as well?
“Yes. Surface processing for electric drive components has clear advantages that are highly relevant to end customers – worth their weight in gold, you might say. Just as for the combustion engine, component surface optimisation in electric drives boosts efficiency and enhances component properties generally. The process is cost-effective by default, but even more so if you use it in a targeted way to focus on the components that cause the most friction. Ultimately it means you can get the same range from a smaller battery or extend the range of the existing one.
Noise emissions, i.e. NVH optimisation, is another key topic in electric drive development because you can hear noises that the combustion engine used to drown out.”
Why should automotive manufacturers consider using OTEC process technology in particular? How does your process have the edge over others?
“Our existing automotive customers are benefiting not only from the component enhancements I’ve already mentioned but also from process advantages. OTEC’s special stream finishing process is acid-free, which is good news for people and the environment. It’s also cheaper than other finishing processes. And with average processing times of 90 seconds, it’s the fastest mass finishing process on the market.
The big difference between OTEC Präzisionsfinish machines and others is the high processing forces and high proportion of frictional energy. In stream finishing, the workpieces are clamped in a holder and lowered into a rotating container filled with an abrasive or polishing medium.
The workpiece rotates and is processed as the medium circulates around it. Stream finishing can remove material faster and more precisely than any other mass finishing process. Our SF range is specially designed for application requirements that existing processes were unable to meet. Repeatability and process time are critical factors in the automotive industry.
The high forces built into our machines can also process thin geometries very effectively using fine grinding and polishing media. And with easily adjustable cycle times and automatic loading options, they’re perfect for integration in production lines.”
Thanks Florian!
It runs like clockwork: SF Series automation with Robot Loading System (RLS)
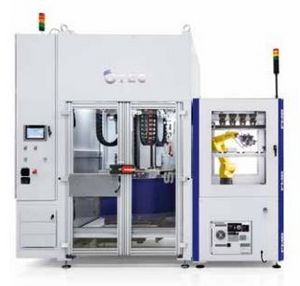
When processing large volumes of workpieces, short loading and set-up times make your operations far more efficient. That’s where our automatic robot loading system comes in (the SF RLS, see left).
SF Automation Series machines can be fitted with optional pulse finishing and work well, for example, in cyclic production lines. Depending on your requirements, the machines can either be set up for automatic loading or fitted with it as an integrated option. The machine design is modular and therefore easy to adjust to cycle time. The SF Automation can thus be easily inte-grated as a key element of any production line.
Free sample processing
Put us to the test: send us some samples and our in-house Finishing Center will specify your pro-cess free of charge. More Information >>
back