Automatic polishing saves time and money
Stay up and running: Tablet tools with flawless surfaces
Tablet pressing can be a complex task depending on tablet formulation and shape. The tools need polishing from time to time because the abrasive pressed powder reacts with and roughens their surface. Polishing counteracts this. A smooth pressing surface reduces friction between the punch and the powder, often increasing production rates as a result. It also reduces the tendency for tablets to stick, and therefore quite literally guarantees smoother processing. Polishing can significantly extend tool life as well as reducing the cost of replacement dies and machine downtime.
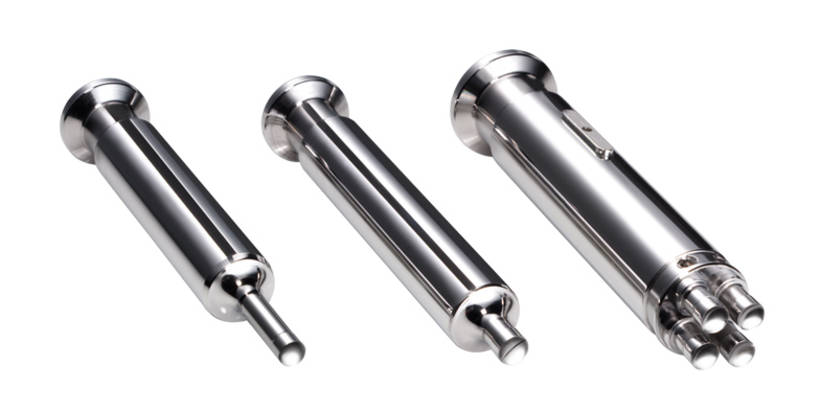
Manual polishing is still common practice today. But the problem with hand finishing is variation: contact pressure, processing time, the quantity of polishing paste used, and so on, all depend on the skills of the person doing the work. In punch sets, these individual variations can cause major inconsistencies in shape fidelity and surface quality. They can even affect the sensors on the press and lead to breaks in production.
The OTEC DF Pharma (DF-P) series features a fast, reliable, tried and tested polishing process. By rotating the punches as they are dragged through polishing granulate, it finishes even the most complex geometries easily and efficiently. And because our process removes only the peaks on rough surfaces, it keeps shapes and dimensions true.
The design, materials and setup of our DF-P machines are specially developed for pharmaceutical production, which is one of the reasons why major pharmaceutical manufacturers all over the world have been them for years.
Polish up to 120 punches simultaneously and automatically – within 30 minutes!
One example of polishing media is a polishing paste with an added granular carrier medium made of plastic. Our polishing process only uses substance mixtures that are tried and tested in pharmaceutical applications, simplifying or indeed dispensing with costly, time-consuming certification. Application-specific workpiece holders are a key factor in perfect processing results. They not only hold workpieces in place more effectively but also speed up fitting, which makes batch changes much easier.
We supply quick-change holders as standard for all common punches including EU and TSM.
Alongside the DF Pharma Series, OTEC provides loading and unloading systems that can be fully automated with robotic integration for long periods of unmanned operation.
back