Optimale Werkzeugbearbeitung? Tauchgleitschleifen (SF) und Electrofinish (EF) im Vergleich
Florian Reinlea, Maximilian Eckla, Luca Wölka, Carlos Barbado Fernándeza, Lukas Göhlera
aOTEC Präzisionsfinish GmbH, Straubenhardt
Abstract
Die präzise Verrundung und Glättung von Werkzeugschneiden ist entscheidend für eine längere Standzeit und stabile Zerspanungsprozesse. In diesem Bericht werden mit dem mechanischen Tauchgleitschleifen im Streamfinish-Verfahren und dem elektrochemischen Electrofinish zwei etablierte Verfahren der Werkzeug-Nachbearbeitung vergleichend untersucht. Streamfinish ermöglicht durch abrasive Bearbeitung einen hohen, gezielt steuerbaren Materialabtrag und eignet sich besonders für größere und mechanisch robustere Werkzeuge. Electrofinish dagegen nutzt anodisches Abtragen in einem Elektrolyt, um ohne mechanische Belastung filigrane oder komplex geformte Werkstücke zu glätten. Beide Verfahren erzielen eine definierte Schneidkantenverrundung, unterscheiden sich jedoch in Wirkmechanismen und Ergebnissen: Streamfinish kann einen einstellbaren K-Faktor von ~0,5 bis ~2,0 realisieren und bei geeigneter Parametrierung erhebliche Druckeigenspannungen sowie Verfestigungen in der Randzone induzieren. Electrofinish erreicht demgegenüber äußerst geringe Rauheiten Werkstücke ohne Eintrag von Verunreinigungen oder mechanischem Umformen und Scheren der Mikrooberfläche. Eigenschaften, die insbesondere bei Mikro- und Präzisions-Werkzeugen vorteilhaft sind. Der Bericht illustriert die spezifischen Stärken beider Verfahren, abschließend wird aufgezeigt, dass eine kombinierte Anwendung von Streamfinish und Electrofinish in der Praxis vielversprechend sein kann, um optimale Ergebnisse in der Werkzeugbearbeitung zu erzielen.
Einleitung
Die Schneidkantenverrundung und Homogenisierung der Schneidkante sind zentrale Maßnahmen zur Steigerung der Werkzeugstandzeit. Sowohl das mechanische Gleitschleifen, insbesondere das Streamfinish-Verfahren, als auch das Electrofinish bieten Möglichkeiten zur gezielten Kantenpräparation. Während das Streamfinish-Verfahren durch seine hohe Materialabtragsleistung und Flexibilität für größere Werkzeuge geeignet ist, spielt das Electrofinish seine Stärken bei filigranen Werkzeugen aus, die mechanischen Kräften nicht standhalten würden. In diesem Bericht werden beide Verfahren detailliert beschrieben, ihre Vor- und Nachteile gegenübergestellt und Anwendungsgebiete beleuchtet.
1. Mechanisches Tauchgleitschleifen: Streamfinish-Verfahren
Das Streamfinish-Verfahren basiert auf einem rotierenden Arbeitsbehälter, in den das Werkzeug in abrasives Granulat eingetaucht wird. Die gezielte Einstellung von Prozessparametern ermöglicht eine kontrollierte Schneidkantenverrundung mit einstellbarem K-Faktor zwischen 0,5 und 2,0. Typischerweise wird ein K-Faktor größer 1 bevorzugt, um eine verbesserte Standzeit und Spanbildung zu gewährleisten.
1.1 Prozessbeschreibung und technische Umsetzung
Tauchgleitschleifen basiert auf einem mit meist abrasivem Schleif- oder Poliergranulat gefüllten drehenden Arbeitsbehälter, in den ein definiert fixiertes Werkstück eingetaucht wird (Abb. 1).
OTEC Präzisionsfinish GmbH hat dieses Verfahren zum Streamfinish (SF) weiterentwickelt. Mit der präzisen Rotation des Werkstückhalters um die eigene Achse werden die Bearbeitungsmöglichkeiten erweitert. Es werden viele Kombinationen der Rotation um die Achsen ermöglicht. Der Werkstückhalter kann zudem um die Längsachse gepulst, d.h. hochdynamisch alternierend, gedreht werden. Die Eintauchtiefe und der Eintauchwinkel bzw. der daraus resultierende Wand- und Bodenabstand sind zentrale Parameter, um die Leistungsfähigkeit des Prozesses einzustellen. Mittels der Prozessparameter kann die Strömung sehr flexibel an die Anforderungen der spezifischen Werkstücke angepasst werden. Dies ermöglicht eine homogene Oberflächenbearbeitung und eine gezielte Kanten- und Schneidkantenpräparation.
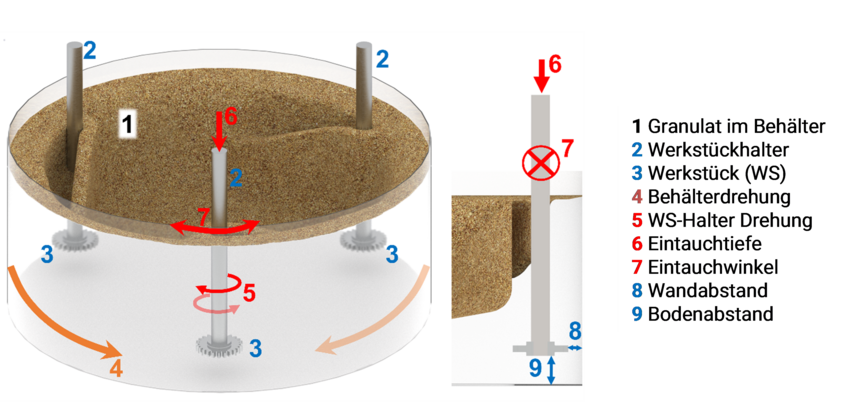
Die Reibenergie entsteht aus dem Druck und der Bewegung des Granulats relativ zum Werkstück. Dieser Energieeintrag des Streamfinish ist günstig für die Oberflächen-Konditionierung [1] und ermöglicht eine durch Scherbeanspruchung induzierte Gefüge-Veränderung, die im Falle von Schnellarbeitsstahl (HSS) auch zur Druckeigenspannungsinduktion führen können. Die langjährige Praxis zeigt, dass das Streamfinish-Verfahren eine hohe Reproduzierbarkeit aufweist und sich flexibel an verschiedene Werkzeug-Geometrien anpassen lässt. Neuerungen wie die digitale Modellierung mittels DEM-Simulation ermöglichen hinsichtlich dieser Stärken weiteres Entwicklungspotential.
1.2 DEM Simulation als virtuelle Abbildung
Gleitschleifprozesse wie das Streamfinish können mittels Diskreter Elemente Methode (DEM) virtuell abgebildet werden. Im Gegensatz zu konventionellen FEM- oder CFD-Methoden werden bei der DEM einzelne, frei bewegliche Partikel simuliert, die miteinander und mit Begrenzungswänden interagieren können [2]. Auf ein statisches Rechengitter, das bei dynamischen Bewegungen kontinuierlich angepasst werden müsste, kann verzichtet werden. In jedem Zeitschritt wird die Wechselwirkung jedes Partikels mit potenziellen Nachbarn und den Wänden (z.B. der Werkstückoberfläche) berechnet. Der Zeitschritt wird so klein gewählt, dass jede Partikelbewegung exakt erfasst wird. Dadurch entfällt die Notwendigkeit, Konvergenzprobleme eines impliziten Lösers zu bewältigen – ein Vorteil expliziter Simulationsmethoden. Die Kräfte zwischen Partikeln und Wand werden aus Relativbewegung, Masse und Trägheit berechnet und um tangentiale Reibungs- sowie Adhäsionskräfte ergänzt. Beim Normalkraftmodell steigt die Kraft mit zunehmender Partikelüberschneidung; das Feder-Dämpfer-Modell erzeugt einen Rückprall, sobald die Gegenkraft nachlässt. In diesem Schritt wird auch die Energieabsorption basierend auf der Stoßzahl modelliert. Diese Simulationsmethode ist sowohl für komplexe Partikelformen, kugelnahe Formen als auch für idealisierte Kugeln geeignet. Eine Abstraktion als Kugel erfordert weniger Rechenaufwand, sodass Millionen Partikel simuliert werden können. Daher steht für annähernd kugelförmige Partikel ein Rollwiderstandsmodell zur Verfügung, um deren effiziente und zugleich realitätsnahe Abbildung zu ermöglichen.
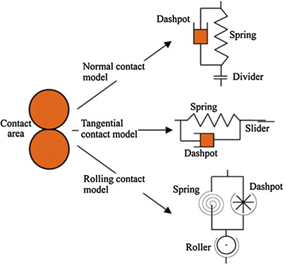
Die Summe quantitativer und visueller Auswertemöglichkeiten einer DEM-Simulation ist vielfältig. Für Validierungssimulationen oder Maschinenbelastungsbetrachtungen werden resultierende Kräfte oder Biegemoment herangezogen, errechnet aus der Summe lokaler Normal- und Tangentialkräfte auf das Werkstück und den Halter. Für anwendungsnahe Optimierungen ist insbesondere die Relativgeschwindigkeit der Partikel zur Werkstückoberfläche interessant sowie das Produkt aus lokalem Druck und Relativgeschwindigkeit. Weder ausreichender Druck noch hohe Geschwindigkeit allein ermöglichen eine effektive Bearbeitung – erst die Kombination beider Größen liefert einen geeigneten Kennwert für den Bearbeitungseffekt. Diese Größe wird als P×V-Wert bezeichnet und stellt ein Leistungsäquivalent des Prozesses dar [4].
2. Electrofinish: Glättung durch anodischen Materialabtrag
Das Electrofinish ermöglicht eine präzise Oberflächenbearbeitung durch anodisches Auflösen des Metalls in Elektrolyten [6]. Besonders bei filigranen Werkzeugen oder Materialien (z.B. Hartmetall) bietet es Vorteile, da nahezu keine mechanische Belastung auf das Werkstück ausgeübt wird.
2.1 Prozessbeschreibung und technische Umsetzung
Das Electrofinish ist ein elektrochemisches Verfahren zur Verringerung der Rauheit metallischer Oberflächen durch gezieltes anodisches Auflösen des Werkstoffs in einem Elektrolyt. Im Gegensatz zum mechanischen Polieren sind hierbei keine abrasiven Mittel erforderlich, die die kristalline Gefügestruktur verändern oder in die Oberfläche eingebracht werden könnten. Somit ist es möglich, empfindliche und komplex geformte Werkstücke ohne Eintrag von Verunreinigungen und ohne mechanische Verformung zu glätten. Diese Vorteile haben in den letzten Jahren zu einer zunehmenden industriellen Anwendung geführt, insbesondere im Bereich medizinischer Implantate und in der Zahnmedizin. Obwohl das Prinzip, eine Oberfläche durch anodisches Auflösen zu glätten, bereits zu Beginn des 20. Jahrhunderts durch Beutel [5] und Spitalski [6] beschrieben wurde, basiert der Großteil der noch heute verwendeten Elektropolierlösungen auf den Studien von Figour [7] und Jacquet [8] aus den 1930er-Jahren. Systematische Untersuchungen während der darauffolgenden Jahrzehnte verdeutlichen, dass das Electrofinish auf die Ausbildung einer diffusionslimitierten Schicht zurückzuführen ist, durch die insbesondere Mikrorauheiten bevorzugt abgetragen werden [9 – 19].
Um eine möglichst glatte und glänzende Oberfläche zu erhalten, müssen der Elektropolierprozess, der Elektrolyt und das Material des Werkstücks gut aufeinander abgestimmt werden [18, 19]. Es existieren zahlreiche Elektrolytsysteme – von Mischungen starker Säuren über neutrale und alkalische bis hin zu nicht-wässrigen Lösungen [20]. Diese zeichnen sich im Allgemeinen dadurch aus, dass die flüssige Elektrolytlösung das Werkstück durch Anlegen anodischer Potentiale auflöst, auf diese Weise Material abträgt und die Oberfläche glättet, weshalb diese als Glanzbäder bezeichnet werden. Nachteile dieser Bäder sind jedoch ihre häufig hohe Korrosivität, der Gehalt an gesundheitsschädlichen Substanzen und die intensive Gasentwicklung an den Elektroden. Zusätzlich werden durch Abschirmung des elektrischen Feldes innenliegende Bereiche komplex geformter Bauteile schlechter bzw. gar nicht bearbeitet. Ein Lösungsansatz hierzu bieten Gemische aus Festkörperpartikeln und Elektrolytflüssigkeit, die eine deutlich bessere und homogenere Bearbeitung der Oberfläche ermöglichen [21, 22]. Dadurch können umweltfreundlichere und weniger korrosive Chemikalien zum Einsatz kommen als bei herkömmlichen Prozessen wie etwa in Glanzbädern

2.2 Vorteile und Grenzen
Ein wichtiger werkstoffspezifischer Aspekt beim Electrofinish von Hartmetall-Werkzeugen ist das Cobalt Leaching – das selektive Auslösen der Kobaltbinderphase. Während einige Experten dies als nachteilig betrachten, sehen andere darin eine Verbesserung der Haftung nachfolgender PVD-Beschichtungen. Eine Reduzierung des Cobalt Leachings auf ein Minimum wird aktuell untersucht.
Ein weiterer Vorteil des Electrofinishs ist die Möglichkeit, bereits aufgebrachte PVD-Beschichtungen zu glätten und damit eine verbesserte finale Oberfläche zu erzielen. Dies geschieht durch Herauslösen der Metallatome, wobei der kovalente Verbindungspartner Sauerstoff oder Stickstoff ausgast. Da diese Beschichtungen häufig sehr resistent gegenüber mechanischem Abtrag sind, ist diese elektrochemische Abtrags-Methode hier besonders vorteilhaft. Bei mechanischem Abtrag kann es zum Herausbrechen von sogenannten Droplets (Schmelzspritzern) der Beschichtung kommen. Dieses Verhalten tritt beim plateauartigen Abtrag durch das Electrofinish nicht auf.
Das Streamfinish unter gezielter Prozessführung ermöglicht ein schonendes Entfernen oder Glätten von Droplets. In Fällen, in denen das Ausbrechen der Droplets unkritisch ist, kann dies gezielt genutzt werden, um Rauheitsspitzen besonders effizient zu reduzieren.
Durch die mittels Electrofinish geringe erzielbare Mikrorauheit wird die Adhäsion der Zerspanungs-Kontaktpartner reduziert und eine optimale Kraftübertragung ermöglicht. Im Vergleich zum Streamfinish erreicht das Electrofinish typischerweise K-Faktoren zwischen 0,7 und 0,9, wodurch es insbesondere für Anwendungen mit Forderung nach symmetrischem Kantenradius oder Verrundung gemäß Wasserfall Charakteristik geeignet ist.
Besonders geeignete Bauteile sind Mirko-Werkzeuge, Werkzeuge mit scharfen Schneiden (Gefahr von Ausbrüchen), Werkzeuge mit spezifischem mechanischen Strömungsschatten, HSS-Gewindebohrer sowie PVD beschichtete Werkzeuge.
3. Vergleich der Verfahren
3.1. Technische Gegenüberstellung
Merkmal | Streamfinish (mechanisch) | Electrofinish (elektrochemisch) |
Materialabtrag | Hoch, gezielt steuerbar | Niedrig, präzise kontrollierbar |
K-Faktor | 0,5 - 2,0 | 0,7 - 0,9 |
Anwendbarkeit | Große Werkzeuge | Kleine, filigrane Werkzeuge |
Homogenisierung | Sehr gut | Exzellent |
Mikrorauheit | Stark reduziert | Minimal |
PVD-Beschichtungsglättung | gut | Sehr gut |
Tabelle 1 Gegenüberstellung der technischen Möglichkeiten basierend auf dem Expertenwissen innerhalb OTEC Präzisionsfinish GmbH |
3.2 Anwendungsbereiche
- Streamfinish ist ideal für Anwendungen, bei denen hoher Materialabtrag erforderlich ist und größere Werkzeuge präzise bearbeitet werden müssen.
- Electrofinish eignet sich hervorragend für empfindliche oder bereits beschichtete Werkzeuge, da es eine herausragende Glättung bei minimalem Abtrag ermöglicht
4. Praxisbeispiele und Fallstudien
4.1 Einsatz in der Werkzeugindustrie
In der industriellen Praxis wird das Streamfinish-Verfahren häufig bei Fräswerkzeugen, Bohrern, Gewindeschneidern und vielen mehr eingesetzt, um insbesondere deren Standzeit zu verlängern. Electrofinish hingegen findet zunehmend Anwendung bei Mikrowerkzeugen, die in der Medizintechnik oder der Uhrenindustrie eingesetzt werden. In Abb. 4 ist beispielshaft eine elektropoliere Werkzeugoberfläche dargestellt. Man kann auftretendes Cobalt Leaching erkennen, die Cobalt-Binderphase im Hartmetall erfuhr im Vergleich zur Wolframcarbid-Phase mehr Abtrag. Zudem deutet sich die äußerst geringe Mikrorauheit so wie die somit tribologisch günstige plateauartige Oberfläche an. Dies unterstreicht den Mehrwert einer Nachbearbeitung selbst bei bereits beschichteten Präzisionswerkzeugen.
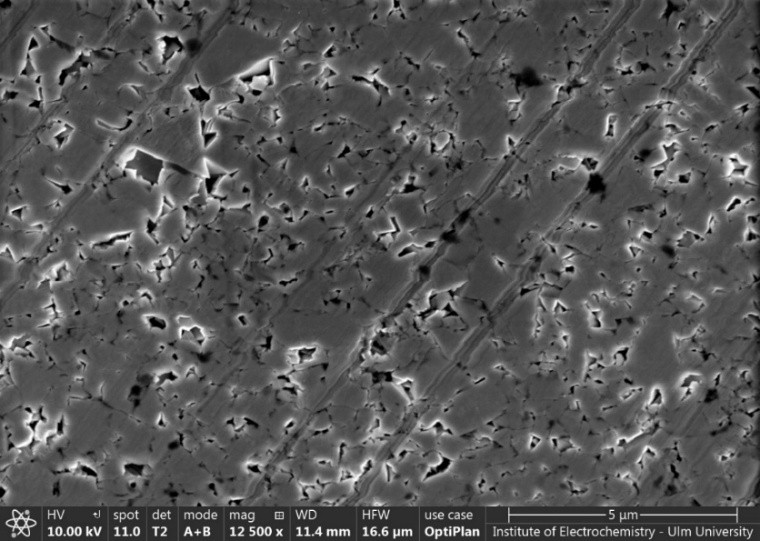
Mit Blick auf das Streamfinish, wie eine umfangreiche Untersuchung mit Vollhartmetall-Fräsern von Zeilmann et al. (2024) dokumentiert, ist eine deutliche Verbesserung der Standzeit mit mittels Streamfinish präparierten Werkzeugen zu erwarten [23].
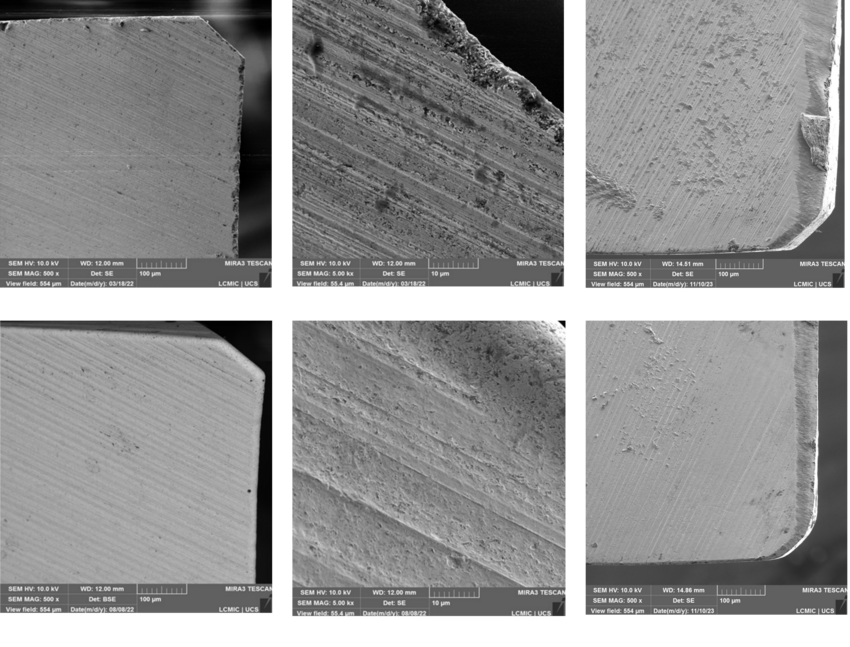
Die beobachteten Steigerungen der Standzeit zeigen eine erwartbare Abhängigkeit vom bearbeiteten Werkstoff, variieren jedoch deutlich: Während bei vergütetem Werkzeugstahl eine Erhöhung um etwa 30 % erreicht wurde, lag sie bei Aluminium bei bis zu 400 %. Dabei ist zu berücksichtigen, dass die eingesetzte Schneidkanten-Verrundung von rund 20 µm nicht optimal auf die Bearbeitung von Stahl ausgelegt war – sie war dafür tendenziell zu groß. Eine stärkere Verrundung erhöht die plastische Werkstoffverdrängung und die Schnittkräfte, was sich bei weniger zähen Werkstoffen wie Aluminium weniger negativ auswirkt [24, 25]. Zusätzlich konnten im Rahmen der Untersuchung eine reduzierte Adhäsionsneigung (vgl. Abb. 6) sowie eine verbesserte Wärmeabfuhr festgestellt werden.
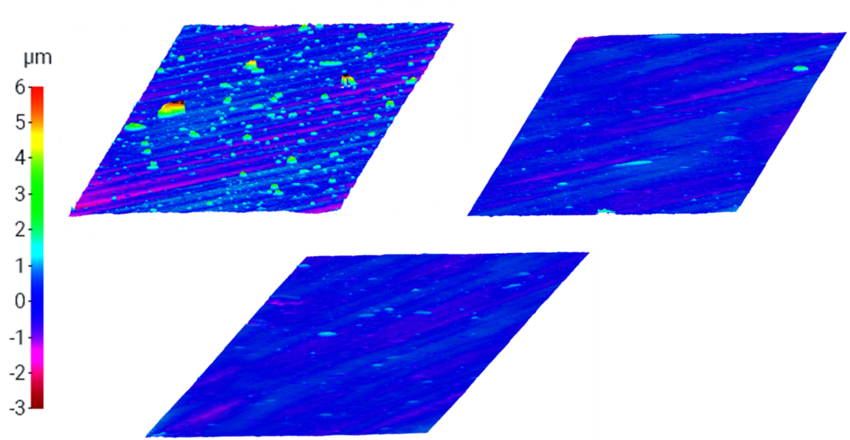
Zum Electrofinish zeigt ein Anwendungsbeispiel anhand eines Gewindebohrers, dass die Rauheit (Flächenparameter Sp) von TiN-beschichteten Werkzeugen um bis zu 80 % reduziert werden kann, was die Werkzeug-Leistungsfähigkeit signifikant verbessert. Ein Vergleich der bearbeiteten Oberfläche zum Ausgangszustand zeigt die deutliche Einglättung der Droplets die bereits nach 2 min fast vollständig entfernt wurden. Dabei reduziert sich die Rauheit um knapp 70% während weitere 60 s die ausreichende Abtragung aller Droplets sicherstellt. Womit sich 80% Reduktion des Spitzenparameters Sp innerhalb von nur 3 min erreichen ließen, zudem kann man den plateauartigen Abtrag erkennen (Abb. 6, m.).
In Summe zeigen diese Beispiele, besonders wie geeignet das Streamfinish als Geometrieverbesserung vor dem Aufbringen der Beschichtung und die Nachbearbeitung zur idealen Anwendungsoberfläche nach dem Beschichten mittels Electrofinish ist. Somit können potenzielle Nachteile der für Werkzeuge neueren Technologie des Electrofinishs vermieden werden und dennoch die Vorteile in Anwendung gebracht werden.
4.2 Wirtschaftliche Betrachtung
Ein weiterer relevanter Aspekt ist die Wirtschaftlichkeit der Verfahren. Während Streamfinish-Anlagen höhere Anfangsinvestitionen erfordern, sind die Stückkosten pro bearbeiteten Bauteil aufgrund kurzer Taktzeiten vergleichsweise niedrig. Electrofinish hingegen benötigt spezielle Elektrolytlösungen und mehr Zeit für vergleichbaren Abtrag was zu höheren variablen Prozesskosten je Werkstück führt. In Anwendungen mit hohem Durchsatz und mechanisch robusten Werkstücken, sowie Vollautomation ist SF daher häufig wirtschaftlicher, während Electrofinish-Anlagen aktuell bei Kleinserien, filigranen Teilen oder besonders in der Endbehandlung nach dem Beschichten ihre Vorteile ausspielen.
5. Fazit und Ausblick
Beide Verfahren – Streamfinish und Electrofinish – haben jeweils spezifische Vorteile. Streamfinish ist prädestiniert für Fälle, in denen ein hoher Materialabtrag und große Kantenverrundungen erforderlich sind oder größere Werkzeuge effizient bearbeitet werden müssen. Überall dort, wo es bereits etabliert ist, bleibt SF eine exzellente Wahl für die Werkzeug- und Kantenpräparation inklusive gezielter K-Faktor-Modifikation.
Electrofinish hingegen eignet sich hervorragend für empfindliche oder komplex geformte sowie bereits beschichtete Werkzeuge, da es eine herausragende Glättung bei minimalem Abtrag ermöglicht. In vielen Fällen kann die hybride Nutzung beider Verfahren – zuerst das Streamfinish, dann das Electrofinish – eine optimale Lösung darstellen, um sowohl makroskopische Formgebung als auch mikroskopische Glättung zu erreichen. Zukünftig könnten Weiterentwicklungen in der Elektrolytformulierung des Electrofinishs dazu beitragen, das Cobalt Leaching weiter zu minimieren. Ebenso könnten neue Prozessstrategien und Parameteroptimierungen das Streamfinish-Verfahren noch gezielter an spezifische Anforderungen anpassen (z.B. angepasstes Kantenprofil für unterschiedliche Werkstoffe). Die Kombination aus digitaler Simulation und experimenteller Optimierung wird weiterhin eine Schlüsselrolle in der Entwicklung fortschrittlicher Werkzeugbearbeitungsprozesse spielen. Letztendlich zeigt der Vergleich, dass weder das mechanische noch das elektrochemische Verfahren allein universell überlegen ist – es kommt auf die richtige Auswahl und Kombination für die jeweilige Anwendungsaufgabe an, um eine optimale Werkzeugperformance zu erreichen. Umfassende Expertise sowohl bei mechanischer als auch bei elektromechanischer Endbearbeitung erhöht die Wahrscheinlichkeit die optimale Kombination der Verfahren für den jeweiligen Anwendungsfall herauszuarbeiten.
Literatur
[1] A. Kacaras, J. Gibmeier, F. Zanger, V. Schulze, Influence of rotational speed on surface states after stream finishing, 4th CIRP Conference on Surface Integrity, 2018
[2] Cundall, P.A., A computer model for simulating progressive, large-scale movements in blocky rock systems. 1971
[3] Zhao T., Coupled DEM-CFD Analyses of Landslide-Induced Debris Flows. 2017
[4] F. Zanger, A. Kacaras, P. Neuenfeldt, V. Schulze, Optimization of the stream finishing process for mechanical surface treatment by numerical and experimental process analysis, CIRP Annals, 2019
[5] E. Beutel in Veröffentlichungen der Chem. Tech. Abteilung des Kais. Königlichen Lehrmittelbüros, Wien, 1907.
[6] Spitalsky, Deutsches Patent Nr. 225.873, 1910.
[7] H. Figour, P. A. Jacquet, Französisches Patent Nr. 707526, 1930.
[8] P. A. Jacquet, Nature 1935, 135, 1076.
[9] J. Edwards, J. Electrochem. Soc. 1953, 100, 189C.
[10] W. C. Elmore, J. Appl. Phys. 1939, 10, 724.
[11] C. L. Faust, J. Electrochem. Soc. 1949, 95, 62C‐72C.
[12] D. R. Gabe, Metallography 1972, 5, 415.
[13] K. B. Hensel, Met. Finish. 2002, 100, 425.
[14] P. A. Jacquet, Metall. Rev. 1956, 1, 157.
[15] C. Wagner, J. Electrochem. Soc. 1954, 101, 225.
[16] J. Toušek, Corros. Sci. 1975, 15, 113.
[17] D. Landolt, Electrochim. Acta 1987, 32, 1.
[18] G. Yang, B. Wang, K. Tawfiq, H. Wei, S. Zhou, G. Chen, Surf. Eng. 2017, 33, 149.
[19] W. Han, F. Fang, Int. J. Mach. Tools Manuf. 2019, 139, 1-23.
[20] M. Buhlert, Electrofinish - elektrolytisches Glänzen, Glätten und Entgraten von Edelstahl, Stahl, Messing, Kupfer, Aluminium und Titan, 2. Aufl., Leuze Verlag, 2017.
[21] N.K. Krioni, A.D. Mingazhev, V.A. Gafarova, J. Phys.: Conf. Ser. 2021, 1891, 012028.
[22] Verdooren, A, Albuquerque G. Advantages and Limitations of Electro-Mechanical Finishing, The Santa Fe Symposium on Jewelry Manufacturing Technology 2009, 2009.
[23] Zeilmann, R. P., & Machining Group (GUS), University of Caxias do Sul. (2024). Tribological Conditions Between Tool and Workpiece for Polished Tools: Final Report 2021–2024. University of Caxias do Sul (UCS)
[24] Denkena, B., & Biermann, D. Cutting edge geometries. CIRP Annals, 63(2), 631–653., 2014
[25] Wang, W., et al. Effect of edge preparation technologies on cutting edge properties and tool performance. Int. J. Adv. Manuf. Technol., 105, 1823–1838, 2019.