DÖRFLER & SCHMIDT AND OTEC PRÄZISIONSFINISH – PRECISION SURFACE PROCESSING FOR SMALL AND VERY SMALL PARTS
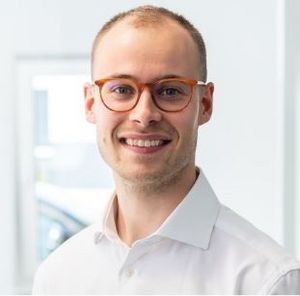
Felix, how long have you been using OTEC machines? And what’s the “human” story behind your relationship with the company?
“We’ve been using OTEC machines ever since 1998. Actually our very first machine was an OTEC. At the time we opted for a CF 3x50. Back then, OTEC’s machines were the best in the business for processing jewellery and watch components. But we mainly used them for deburring and polishing automotive components. That’s still our core business today.”
Would you say that your company has grown alongside OTEC?
“Absolutely. After our first CF3x50, we expanded our capabilities pretty quickly with additional disc finishing machines from OTEC. And we’ve reaped the benefits of OTEC’s continuous development and high quality. We now have over a dozen disc finishing machines. Then, when OTEC brought yet another innovation to market with the stream finishing process, we expanded our offering again with the new technology. That opened up a lot more application areas. More recently, we adopted the new pulse finishing system, which once again is cutting-edge technology.”
Aside from automotive components, what kinds of parts does Dörfler & Schmidt process with OTEC machines?
“We use them to deburr and polish a wide range of materials, mainly metals and plastics, but also ceramics and wood. We use the DF, stream finish and pulse finish machines to deburr, round and polish components that mustn’t come into contact with each other. Most often stamping, forming, milling and cutting tools, but also decorative components.”
What’s the specific benefit of the OTEC stream finishing process for your customers in the toolmaking industry?
“Well, for instance, it really boosts the quality of stamping and forming tools. The surface processing reduces the friction coefficient, which in turn reduces wear on the tool surface. Polishing forming surfaces extends the service life of stamping and forming tools as well as improving machining results. Smoothing off roughness peaks improves forming by reducing the effort required and enhancing flow properties. Surface processing with OTEC machines not only saves on cost-intensive manual work but also guarantees process reliability. Our customers really appreciate that.”
Are there certain orders for which you will only use OTEC machines?
And what are the advantages for you as a service provider?
“I’d highlight the fact that disc finishing on very small parts only works if there’s no gap. OTEC CF machines provide that very feature. So we can deburr, smooth and polish extremely intricate or thin components cost-effectively.
These days, thanks to OTEC technology, we serve a wide range of industries including automotive, medical devices, mechanical and plant engineering, toolmaking, electricals, aerospace, and fashion and jewellery.”
As a service provider, you’re also familiar with machines and processes from other manufacturers. Based on your experience, how would you say they compare with OTEC?
“For a start, production workers find OTEC systems easy and intuitive to operate. But at the same time, it’s possible to customise many of the parameters and to store programs.
That’s key for us as a service provider, because we process countless different parts that require a very wide range of machine parameters for the best results. Another advantage is the high processing quality and long service life we get with OTEC machines.”
After working with OTEC for over 20 years, what do you value most about the relationship?
“Above all, it’s the fact that we work together so closely. That means we can discuss technical issues at a high level, and OTEC’s door is always open – they’re always ready to help. We’ve built up a really good, friendly relationship with lots of OTEC employees.”
Thanks for such a candid interview Felix.
All the best to you and your customers!
About Dörfler & Schmidt Präzisionsfinish: Quality awareness & environmental awareness
Dörfler&Schmidt Präzisionsfinish provides deburring, rounding and polishing services for metal and plastic parts, using mass finishing, double-face grinding, stream finishing and brushing processes. The company has been using OTEC mass finishing machines for over 20 years, thanks to their fast, cost-effective and consistently high surface finishing results. Dörfler &Schmidt is certified under the ISO 9001 quality standard and ensures its entire process chain is environmentally friendly. For example, all process water is continuously treated and recycled. It also obtains over 45 percent of its electricity through carbon-free solar energy.
Contact details: https://doerfler-schmidt.de/
About OTEC Präzisionsfinish
OTEC GmbH supplies precision technology for achieving perfect surfaces in the tooling, medical device, jewellery, automotive and aerospace industries, among others. OTEC machines are used for smoothing, precision edge-rounding, polishing and deburring a wide variety of workpieces, with the aim of improving surface quality. With a network of international business partners, OTEC has a global presence. A wide range of industries benefit from OTEC’s market-leading and in-depth technical expertise when it comes to developing the perfect interplay of machine and abrasive.
Press contact
OTEC Präzisionsfinish GmbH
Heinrich-Hertz-Straße 24
75334 Straubenhardt-Conweiler Germany
Tel. + 49 (0) 70 82 - 49 11 20 | Fax + 49 (0) 70 82 - 49 11 29
info(at)otec.de | www.otec.de