Effective evironmental protection and cost reductions
with OTEC's centrifuge technology
Be smart: Use water treatment!
OTEC is leading in the recirculation of process water with centrifuge technology in mass finishing. OTEC’s process water centrifuges can be linked up with existing or new mass finishing machines about to be installed and provide the necessary control and process technology. Thomas Gegenheimer, Project Manager for Systems and and Special-Purpose Machinery at OTEC states:
„OTEC’s centrifugal water recirculation systems can save over 95% of the costs for fresh water supply and waste water - a significant reduction in costs and environmental impact. We offer process water centrifuges in different sizes to suit different needs.“
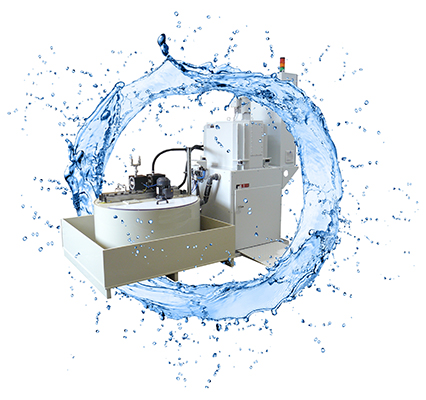
Waste not - reuse!
Process water (marked red) is fed into the centrifuge. The treated water (marked in blue) is recycled back into the process.
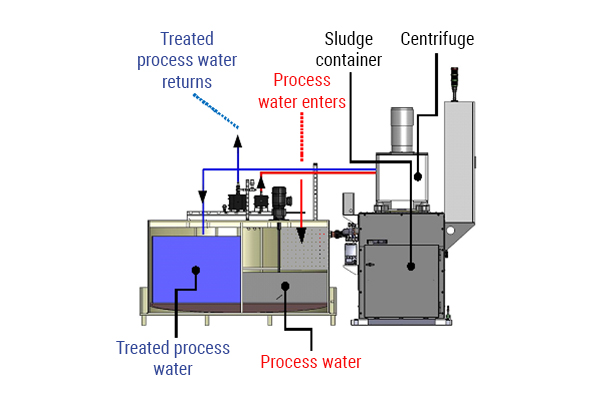
The centrifuge works by separating particles from the process water using centrifugal force. The particles are compressed into sludge, which is collected in the centrifuge container. The sludge is then removed manually or automatically depending on the model and can be disposed of correctly afterwards.
Adding suitable process water purifiers helps to separate the solids effectively and thoroughly and ensures that the sludge contains very little water residue so that it meets the standard requirements for disposal.
Thomas Gegenheimer shares some useful advice from his many years of project experience: "The automatic model removes sludge at least every four hours, which really pays off as it significantly reduces the person-hours required. Depending on the centrifuge’s capacity, several mass finishing machines can also be linked up to one centrifuge.”
Benefits of mass finishing with water recirculation systems
Processing using OTEC’s mass finishing machines with water recirculation systems has many standout benefits across the board for our customers:
- By recycling the process water, fresh water use is reduced by 90%
- Compound savings of up to 80 % compared with fresh water operation
- Sustainable reduction of waste water
- Minimal use of process chemicals (compounds and water purifiers)
- No obligatory authorisation or monitoring for recirculating process water treatment systems
- No obligatory monitoring or documentation for recirculation systems required by official authorities
Optimum working conditions
Both the quality of the process water and of the compounds used ensure that the entire system is constantly reliable.
Process water should have a hardness of between 4 and 15 dH, which is generally the case by virtue of the quality of the fresh water used. If it is not, treatment agents can be added to achieve the right water hardness.
When defining the process, it is important to choose compounds that, due to their chemical composition and long-term usability, are suitable for recirculation in aqueous systems. The quantities of compound used are low and can be documented during straightforward monitoring measures and regulated using manual or automatic dosing. Because the compounds have very low foaming tendencies, the process is highly reliable even under the high mechanical loads caused by the centrifuges.
Are you ready for resource- and cost-efficient processes?
With over 25 years of experience in mass finishing and process development, we are always happy to offer our expert advice as to which of our proven process water treatment solutions will deliver the best results for your mass finishing machines. We can create sophisticated and sustainable integrated approaches that are in line with current environmental protection and modern quality management systems as well as providing maximum cost-effectiveness and process reliability.
Your OTEC expert is Kevin Rastetter:
Tel: + 49 (0) 70 82 / 49 11 7214, E-Mail: k.rastetter@otec.de