MECHANICALLY DEBURRED AND ROUNDED SLIDES AND BOLT CARRIERS FOR RELIABLE FIRING
Success-Story firearms
Subtractive manufacturing in firearms production can leave burrs and sharp edges on pistol slides and rifle bolt carriers. Unless these are properly removed, there is no guarantee that the gun will operate reliably and correctly. In this case study we focus on pistol slides, but the information applies to bolt carriers in the same way.
The firing function is crucial
In shooting sports, competitors must be able to guarantee faultless firing if they want to win. In the defence sector, reliable firearms in perfect working order are a matter of life and death. Imprecisely removed burrs and edges can cause the slide to tilt during loading. This can damage the gun when fired. Worse still, it may not fire at all.
Maximum precision for flawless internal geometries
In some cases, firearms manufacturers have to contend with highly inconsistent, unsatisfactory de-burring and rounding results that have an impact on quality. These are usually manual, consecutive processes and therefore very labour-intensive. At the same time, highly specialised manual debur-ring skills are in short supply: employees with decades of experience are moving into other fields of work, and manual trades are in decline. The shift towards fully automated processes is gaining ground, but many of them are not designed to reach internal geometries effectively.
It was this backdrop that prompted one of our customers to look for an automated process explicitly engineered for reliable deburring and reproducible edge rounding in the hard-to-access internal ge-ometries on pistol slides. The company evaluated various techniques such as thermal deburring, trough vibration and electrochemical deburring. However, these methods either fell short of the draw-ing specifications, or were not automated, or were cost-intensive to implement. But the firm finally found what it was looking for: our stream finishing process produced the best results in the shortest process time and at the highest level of reproducibility – all of which made it the most cost-effective option compared with the others.
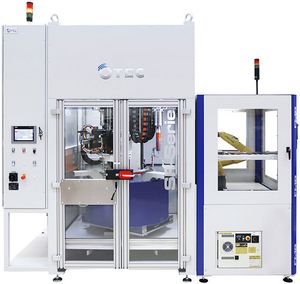
Stream finishing - smooth firing
Courtesy of its new stream finishing machine, the sports gunmaker is now achieving the exacting surface requirements it was aiming for. By attaching a slide to each processing spindle, it can finish three individual slides in one machine in a matter of minutes. And with robot-automated loading, the machinery can operate unmanned for long periods.
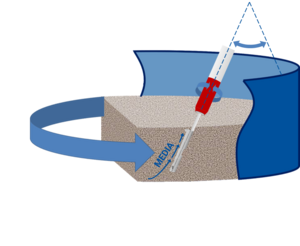
The first step is to position the slide at specific angles in the process container. Superfine media then flows through the firearm component, precisely targeting burrs and sharp edges in the hard-to-reach internal geometry. In step two, the external geometries are precision deburred, rounded and de-lustred. After surface processing with OTEC stream finishing, the slides are ready for downstream production stages such as tempering and burnishing.
OTEC Defence Industry Manager Adrian Kofler oversaw the entire project from initial tests to machine acceptance. He sums up the story:
“The sports gun manufacturer opted for our stream finishing process after testing numerous other methods that just couldn’t produce the required results, or took too long and therefore weren’t cost effective. Our customer evaluated a variety of processes before finally finding one that could finish the slide’s internal geometries to such a demanding quali-ty level. The new process has also been very well received by the production employees who previously did the manual work. OTEC’s technology has made a welcome and significant contribution to occupational health and safety by taking the physical strain out of their job.”
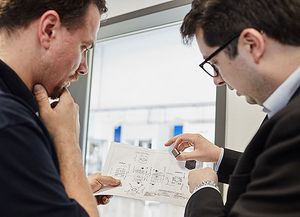
Define your component process with the help of OTEC Präzisionsfinish Experts
Our specialist team at the OTEC Finishing Center is ready to assist in defining your process – what-ever the tool geometry, surface structure or edge-rounding requirements. Work with us to identify exactly the right process for your component. Book your sample processing experience today.